Герметичные устройства и установки
Безопасность эксплуатации герметичных систем, находящихся под давлением
Безопасность эксплуатации герметичных систем, находящихся под давлением
Герметичность — это непроницаемость жидкостями и газами стенок и соединений, ограничивающих внутренние объемы устройств и установок.
Принцип герметичности, т. е. непроницаемости, в той или иной мере используется практически во всех устройствах и установках, в которых в качестве рабочего тела применяется жидкость или газ. Этот принцип является также обязательным для вакуумных установок. Устройства и установки, использующие в процессе работы принцип герметичности, можно сокращенно называть герметичными.
Внутренние объемы герметичных устройств и установок ограничивают среду, которая может выполнять существенно различные функции: она может быть либо рабочим телом, либо исполнять роль той среды, в которой протекают основные рабочие процессы. Поэтому параметры ее состояния (как и сама среда) весьма различна. Например, среда может быть сильно нагретой — иметь температуру несколько тысяч градусов — или быть сильно охлажденной — иметь температуру, близкую к абсолютному нулю; давление внутри устройства может измеряться тысячами атмосфер или иметь значения порядка 10-13 мм. рт. ст.
В ряде случаев нарушение герметичности, т. е. разгерметизация устройств и установок не только нежелательна с чисто технической точки зрения, но и опасна для обслуживающего персонала и производства в целом.
Во-первых, нарушение, герметичности может быть связано со взрывом. Здесь также следует различать два момента. С одной стороны, взрыв может являться причиной нарушения герметичности, например, воспламенение взрывчатой смеси внутри установки. С другой стороны, нарушение герметичности может стать причиной взрыва, например, при нарушении герметичности ацетиленового трубопровода, вблизи участков нарушения образуется ацетилоновоздушная смесь, которая может быть подожжена самыми слабыми импульсами. Незамеченное длительное горение приводит к такому сильному разогреву газохода, что ацетилен в нем самовоспламеняется.
Во-вторых, при разгерметизации появляются опасности, зависящие от физико-химических свойств изолированной рабочей среды. Ими могут быть:
1) радиационная опасность, возникающая, например, при использовании в установках в качестве теплоносителя жидких радиоактивных металлов, обладающих высоким уровнем ионизирующего излучения;
2) опасность получения ожогов под воздействием высоких или, наоборот, низких температур (термические ожоги) и из-за агрессивности среды (химические ожоги);
3) опасность травматизма, связанная с высоким давлением газа в системе, например, нарушение герметичности баллона с газом при давлении 200 атм отверстием диаметром 15 мм приведет к появлению начальной реактивной тяги около 350 кгс; при массе баллона 70 кг он может приобрести ускорение, равное 5g и переместиться на некоторое расстояние;
4) опасность отравления, связанная с применением инертных и токсичных газов и др.
Таким образом, принцип герметичности, используемый при организации рабочего процесса ряда устройств и установок, является одновременно важным с точки зрения безопасности их эксплуатации и, следовательно, инженерный комплекс охраны труда должен быть направлен на его поддержание.
Из множества герметичных устройств и установок можно выделить те, которые имеют наиболее широкое применение в промышленности. К ним следует отнести:
Трубопроводы. Трубопроводы — устройства для транспортировки жидкостей и газов.
Жидкости и газы разбиты на следующие десять укрупненных групп в соответствии с которыми установлена опознавательная окраска трубопроводов:
Номер группы и вещество | Цвет познавательной окраски |
1. Вода
2. Пар 3. Воздух 4. Газы горючие 5. Газы негорючие 6. Кислоты 7. Щелочи 8. Жидкости горючие 9. Жидкости негорючие 10. Прочие вещества | Зеленый
Красный Синий Желтый Желтый Оранжевый Фиолетовый Коричневый Коричневый Серый |
Количество предупреждающих колец какого-либо цвета должно соответствовать степени опасности транспортируемого вещества для людей или предприятия.
Кроме цветных сигнальных колец применяют также предупреждающие знаки, маркировочные щитки и надписи на трубопроводах (цифровое обозначение вещества, слово «Вакуум» для вакуум-проводов, стрелки, указывающие направление движения жидкости и др.).
Баллоны для хранения и перевозки сжатых, сжиженных и растворенных газов при температурах от —50 до +60° С. Баллоны изготовляют малой емкости от 0,4 до 12 л, средней — от 20 до 50 л и большой емкости от 80 до 500 л. Наибольшее распространение имеют баллоны емкостью 40 и 50 л.
Баллоны малой и средней емкости изготовляют на рабочие давления * 100, 150 и 200 кгс/см2 из углеродистой стали и на рабочие давления 150 и 200 кгс/см2 из легированной стали.
Для того чтобы легко и быстро распознавать баллоны, предназначенные для определенных газов, предупреждать их ошибочное наполнение и предохранять наружную поверхность от коррозии, на заводах-изготовителях баллоны окрашивают в установленные стандартом цвета, наносят соответствующие надписи и отличительные полосы. Кроме того, у горловины каждого баллона на сферической части должны быть отчетливо выбиты следующие данные: товарный знак предприятия-изготовителя; номер баллона по системе нумерации предприятия-изготовителя; дата (месяц, год) изготовления (испытания) и год следующего испытания в соответствии с правилами Госгортехнадзора (например, при изготовлении баллонов в марте 1975 г. и последующем их испытании в марте 1980 г. ставят клеймо 3-75-80); вид термообработки (N — нормализация, V — закалка с отпуском); рабочее и пробное гидравлическое давления в кгс/см2; емкость баллона в л; масса баллона в кг; клеймо ОТК; обозначение действующего стандарта.
Баллоны для сжатых газов, принимаемые заводами-наполнителями от потребителей, должны иметь остаточное давление не менее 0,5 кгс/см2, а баллоны для растворенного ацетилена — не менее 0,5 и не более 1 кгс/см2. Остаточное давление позволяет определить, какой газ находится в баллонах, проверить герметичность баллона и его арматуры и гарантировать непроникновение в баллон другого газа или жидкости. Кроме того, остаточное давление в баллонах для ацетилена препятствует уносу ацетона — растворителя ацетилена (при меньшем давлении унос ацетона увеличивается, а уменьшение количества ацетона в баллоне повышает взрывоопасность ацетилена).
Сосуды для сжиженных газов. Сжиженные газы хранят и перевозят в стационарных и транспортных сосудах (цистернах), снабженных высокоэффективной тепловой изоляцией.
Для хранения и транспортирования небольших количеств сжиженных газов (кислорода, аргона, азота и воздуха) по ГОСТ 16024—70 изготовляют сосуды Дьюара из алюминиевого сплава типа АСД шаровой и цилиндрической форм емкостью 5, 16, 25 и 100 л.
Для охлаждения и хранения различных предметов в среде сжиженных газов изготовляют сосуды Дьюара типа ЦСД цилиндрической формы емкостью 5, 10, 16 и 50 л.
После засыпки межстенного пространства сосуда порошковой экранированной изоляцией (аэрогель с бронзовой пудрой) воздух из него откачивается до остаточного давления 1 • 10-1 — 2 • 10-1 мм рт. ст. Внутри вакуумного пространства помещена камера с адсорбентом (силикагелем, цеолитом) для поглощения остаточных газов и понижения остаточного давления в межстенном пространстве до (1 — 5) • 10-3 мм рт. ст.
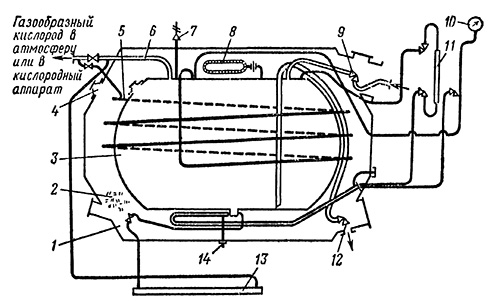
Рис. 78. Схема стационарной цистерны жидкого кислорода емкостью 6000 дм3: — кожух; 2 — изоляция; 3 — сосуд для жидкого кислорода; 4 — предохранительная мембрана кожуха; 5 — змеевик; 6 — труба для отвода паров кислорода; 7 — предохранительный клапан; 8 — перфорированное кольцо; 9 — вентиль для наполнения цистерны кислородом; 10 — манометр; 11 — указатель уровня; 12 — вентиль для слива жидкости; 13 — испаритель; 14 — пробка для продувки отстойника
Стационарный резервуар (рис. 78) представляет собой тонкостенный сосуд 5, подвешенный на цепях в кожухе 1.
В верхней части сосуда имеется люк для осмотра. Кожух снабжен съемной крышкой. Снизу с наружной стороны сосуд имеет отстойник для грязи и масла. От отстойника наружу выведена трубка с пробкой 14 для продувки и удаления грязи. Между стенками кожуха и сосуда находится слой насыпной вакуумно-порошковой изоляции 2. Сосуд наполняется сжиженным газом через вентиль 9. Слив жидкости производят через вентиль 12, установленный на трубе, доходящей до дна сосуда 3. К вентилю присоединен гибкий металлический рукав, другой конец которого соединен с транспортным танком. Сжиженный газ вытесняется через сливную трубу и вентиль 12 давлением паров в сосуде.
Давление паров на время слива жидкости можно повысить. Для этого часть жидкости необходимо испарить в испарителе 13. Жидкость поступает в испаритель через вентиль, а образующийся газ по трубке 6 направляется в верхнюю часть сосуда. Для отвода газа в газгольдер служит змеевик 5, проложенный в изоляции для ее охлаждения. Цистерна снабжена манометром 10, указателем уровня жидкости 11, предохранительной мембраной 4 и предохранительным клапаном 7.
Стационарные резервуары изготовляют емкостью до 500 000 л, а в отдельных случаях и более. В зависимости от конструкции они строятся цилиндрической (горизонтальные и вертикальные) и шарообразной формы. Основные параметры и размеры внутренних резервуаров для сжиженных газов регламентированы ГОСТ 16023—70.
Транспортные сосуды (цистерны) обычно имеют емкость до 35 000 л. Наружная поверхность резервуаров окрашивается эмалью, масляной или алюминиевой красками в светло-серый цвет. На транспортных сосудах наносятся также надписи и отличительные полосы в соответствии с табл. 18.
Таблица 18. Маркировка транспортных резервуаров
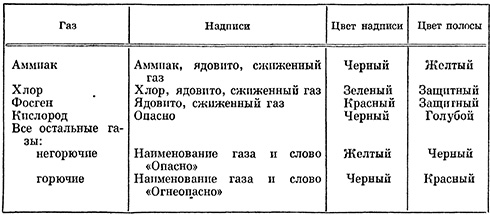
Газгольдеры. Газгольдеры могут быть низкого (постоянного) и высокого (переменного) давления.
Газгольдеры высокого давления (реципиенты) служат для создания запаса газа высокого давления. Расходуемый из них газ проходит через редуктор, который понижает давление газа до требуемой величины и поддерживает его постоянным (обычно менее 15 кгс/см2) в течение всего времени подачи газа в трубопровод потребителя (на резку металла, в мартеновскую печь и т. д.). Реципиенты обычно собирают из баллонов емкостью 400 л (ГОСТ 9731—61).
Газгольдеры низкого давления (150—400 мм вод. ст.) имеют емкость от 10б до 3 • 107 л и применяют для хранения запаса газа, сглаживания пульсаций, выдачи газов, отделения механических примесей и других целей.
Кроме герметичных устройств и установок, рассмотренных выше, в промышленности нашли широкое применение сосуды, предназначенные для ведения химических и тепловых процессов, компрессоры, котлы. Поэтому в нашей стране действуют: «Правила устройства и безопасной эксплуатации стационарных компрессорных установок, воздухопроводов и газопроводов», «Правила устройства и безопасной эксплуатации оборудования атомных электростанций, опытных и исследовательских ядерных реакторов и установок», «Правила устройства и безопасной эксплуатации сосудов, работающих под давлением» и др. В действующих правилах указано, какие устройства и установки до пуска в работу подлежат регистрации в местных органах Госгортехнадзора, и для них определен порядок прохождения периодических и внеочередных технических освидетельствований.
Анализ показывает, что разгерметизация устройств и установок происходит в результате действия целого ряда факторов, которые можно условно подразделить па две группы — эксплуатационные и технологические.
Первые обусловлены физико-химическими свойствами рабочего тела, параметрами его состояния, условиями эксплуатации и т. д. К ним, например, относятся: протекание побочных процессов в устройствах и установках, приводящих к ослаблению прочности конструкции; образование в рабочий период взрывчатых смесей, неправильная эксплуатация и др.
Вторые связаны с технологией изготовления устройств и установок, их транспортировкой и хранением. К ним относятся различные виды дефектов.
Ниже более подробно рассматриваются сначала эксплуатационные, затем технологические факторы разгерметизации.


Полезная информация: