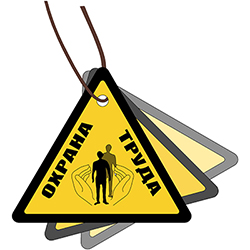
Сварка, наплавка, резка, напыление и пайка металлов сопровождаются наличием ряда вредных и опасных производственных факторов. Сварочные работы могут проводиться на механизированных линиях или конвейерах, на стапелях, открытом воздухе или в помещениях, на различных высотах, под водой и даже в космосе.
Практически при всех видах сварки, при резке и наплавке присутствуют такие опасные факторы, как пыль, газ, световое излучение, высокая температура, тепловое и ультрафиолетовое излучения. Наличие при сварке горючих газов может привести к химическому взрыву, а эксплуатация сосудов под давлением с инертными газами может вызвать физический взрыв. Открытые газовое пламя и дуга, струя плазмы, брызги жидкого металла и шлака при сварке и резке создают опасность ожогов и повышают опасность возникновения взрыва и пожара.
Как правило, сварочные работы должны проводиться в отдельных помещениях, а при электронно-лучевой, диффузионной сварке, плазменной обработке — только в отдельном помещении или изолированном участке цеха. Объем производственных помещений на одного работающего должен быть не менее 15 м3 при площади не менее 4,5 м2, а для плазменной обработки — не менее 10 м2, исключая площадь, занимаемую оборудованием и проходами. При применении лазеров IV класса входные двери помещений должны иметь блокировку. Помещения должны строиться из несгораемых материалов в соответствии с СНиП 2.09.02—85*, СНиП 21.01—97.
Окраска оборудования и помещений для сварки должна быть светлых тонов с диффузным отражением света. Для освещения мест сварки применяют газоразрядные лампы. При выполнении сварочных работ в общем помещении места сварки должны ограждаться ширмами.
Электросварочные устройства должны соответствовать ГОСТ 12.2.003—91*; ГОСТ 12.2.007.0—75*; ГОСТ 12.2.007.8—75*; ГОСТ 12.2.049—80; ГОСТ 12.2.051—80.
Напряжение холостого хода источника тока для дуговой сварки при номинальном напряжении сети не должно превышать: 80 В эффективного значения — для источников переменного тока ручной дуговой и полуавтоматической сварки; 140 В эффективного значения — для источников переменного тока автоматической сварки.
Вредные и опасные факторы при сварочных работах
Ограничитель напряжения холостого хода устройств для ручной дуговой сварки на переменном токе должен снижать напряжение холостого хода на выходных зажимах сварочной цепи до 12 В не позже, чем через одну секунду после размыкания сварочной цепи.
Напряжение холостого хода источника тока для плазменной обработки при номинальном напряжении сети не должно превышать: 180 В — для устройств ручной резки, плазменной сварки или наплавки; 300 В — для устройств полуавтоматической резки или напыления; 500 В — для устройств автоматической резки.
Устройства для электронно-лучевой сварки должны обеспечивать защиту оператора и от рентгеновского излучения. Конструкция такой защиты должна быть неотъемлемой от устройства.
Технологические процессы должны удовлетворять требованиям ГОСТ 12.3:002—75*; ГОСТ 12.3.003—86; Правилам устройства электроустановок (ПУЭ).
При сварке изделий массой более 20 кг должны применяться грузоподъемные устройства. Ширина проходов между оборудованием, движущимися механизмами и перемещаемыми деталями, а также между стационарными источниками питания должна быть не менее 1,5 м; расстояние между автоматическими сварочными установками — не менее 2 м.
Длина первичной цепи между источником питания и первичной сварочной установкой не должна превышать 10 м. Изоляция проводов должна быть защищена от механических повреждений.
Места, где происходят технологические процессы, связанные с высоким уровнем шума, должны укрываться кожухами. Если по условиям технологического процесса невозможно устройство звукоизолирующих кожухов на установки, то операторы должны находиться в звукоизолированных кабинах со смотровыми окнами и дистанционным управлением процессом. Помещения сварки, резки или плазменной обработки в таких случаях должны иметь хорошую звукоизоляцию для защиты смежных участков.
Для уменьшения выделения вредных веществ поверхности свариваемых и наплавляемых изделий, покрытые антикоррозионными грунтовками, необходимо предварительно зачищать от фунта по ширине не менее 100 мм от места сварки.
Защита от тепловых излучений должна осуществляться путем экранирования источника излучения, применения кабин или поверхностей с радиационным охлаждением, воздушного душирования или сокращением времени пребывания в зоне воздействия источников теплового излучения.
Для защиты от вредного действия электромагнитных полей применяются специальные заземленные экраны в виде щитов из металлической сетки (их защитное действие основано на эффекте ослабления электрического поля вблизи заземленного металлического предмета). Экраны могут быть постоянные и переносные в виде козырьков, навесов, перегородок. Экраны следует устанавливать на достаточном расстоянии от токоведущих частей электрооборудования во избежание перекрытия воздушных промежутков. Эти расстояния предусмотрены ПУЭ. В отдельных случаях в качестве защитного средства применяют экранирующий костюм.
Для защиты от поражения электрическим током все установки должны быть заземлены в соответствии с ГОСТ 12.1.030—81*. Элементы сварочной цепи, отрезки кабелей при наращивании должны быть соединены разъемными соединительными муфтами. Нельзя соединять сварочные цепи скрутками с оголенным кабелем. Токоведущие кабели сварочной цепи должны быть изолированы по всей длине и защищены от механического повреждения.
Запрещается использование в качестве обратного провода сети заземления металлических строительных конструкций здания, коммуникаций. Соединение между собой отдельных элементов, используемых в качестве обратного провода, должно выполняться тщательно (сваркой или зажимом).
Наиболее опасными являются работы в замкнутых емкостях. Электросварщик, выполняющий сварочные работы внутри замкнутых емкостей, должен пользоваться диэлектрическими перчатками, галошами, ковриком и шлемом. Работать с металлическим щитком в этом случае запрещено, так как свариваемый объект во время сварочных работ находится под напряжением. Для снятия напряжения в сварочную цепь следует включать аппарат снятия напряжения, который автоматически отключает силовую цепь при разрыве дуги. Работы в замкнутых емкостях должны производиться сварщиком под контролем наблюдающего, который находится снаружи. Сварщик внутри емкости должен быть снабжен предохранительным поясом с веревкой, конец которой длиной не менее 2 м должен быть в руках у наблюдающего.
Во всех случаях производства сварочных работ необходимо применение местных отсосов. При образовании высокотоксичных веществ производство работ без местной вентиляции недопустимо. Это относится к сварке цветных металлов, специальных сталей и черных металлов с покрытиями, плазменной обработке, пайке и лужению. Всасывающие отверстия должны располагаться как можно ближе к месту сварки, так как скорость воздушного потока при удалении от всасывающего отверстия падает примерно обратно пропорционально квадрату расстояния.
Если технологический процесс не позволяет расположить приемник вредных веществ вблизи источника загрязнения, то следует применять сочетание отсосов с местной приточной вентиляцией, воздушными душами или подачей чистого воздуха под маску сварщика.
При сварочных работах внутри замкнутых емкостей следует устраивать местную вентиляцию с выбросом удаляемого воздуха наружу вне зоны забора приточного воздуха. При сварочных работах с применением сжиженных газов (пропана, бутана и углекислого газа) вытяжная вентиляция должна иметь отсос снизу. В случае необходимости сварку внутри емкости ведут в шланговых противогазах и респираторах.
Так как при сварочных работах выделяется большое количество токсичных веществ, то вся вытяжная вентиляция от постоянных рабочих мест должна иметь систему пылеулавливания и нейтрализации загрязнений.