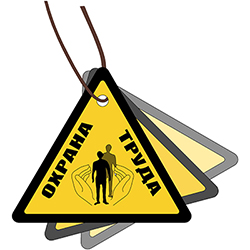
Движение воздуха в окрасочной камере обеспечивается вентиляционными устройствами для подачи чистого и удаления загрязненного воздуха. Для подачи приточного воздуха в верхней части камеры расположен специальный приточный короб (подшивной потолок), нижняя поверхность которого одновременно служит потолком камеры. Приточный короб, нижняя часть которого выполнена из стального перфорированного листа, заполнен тонким фильтрующим материалом. Перфорированный лист выполнен съемным для чистки фильтра.
Очищенный воздух рекуператора по специальному воздуховоду поступает в приточный короб и через потолок-фильтр поступает в рабочее пространство, оттесняя порошок, распыленный вне детали, в нижнюю часть камеры. Порошок, который при распылении не попадает на окрашиваемое изделие, под действием силы тяжести и вертикального потока вентиляционного воздуха попадает в нижнюю часть камеры. Загрязненный порошком воздух удаляется из камеры через всасывающее отверстие щелевидной формы, расположенное на дне камеры, и поступает по отсасывающему воздуховоду на рекуперацию.
Для предотвращения выбивания вредностей из рабочего проема камеры в окружающее пространство предусмотрена воздушная завеса, которая создается путем подачи воздуха из приточного короба через щелевидное отверстие, расположенное вдоль верхней стороны рабочего проема, по схеме «сверху вниз». Начальная скорость истечения воздуха в воздушной завесе регулируется изменением ширины приточной щели.
В табл. 26 приведены сводные результаты по аэродинамическим испытаниям системы вентиляции окрасочной камеры. Нанесение порошкового материала осуществлялось на изделия размерами 700X200X400 мм. Применялся полиэфирный порошок марки П-ПЭ-11 ЗОу черного цвета. При напылении изучалось содержание в воздухе пыли. Полученные данные сведены в табл. 27.
Таблица 26. Результаты замеров параметров воздуха системы вентиляции камеры для ручного напыления порошков
Таблица 27. Содержание пыли в воздухе при нанесении порошка на изделия венгерским электрораспылителем
Анализ содержания пыли в воздухе показывает, что рабочая зона маляра загрязняется пылью в значительных количествах, при этом ее концентрации зависят от производительности распылителя и организации воздухообмена в камере. При производительности 50 г/мин и включенном притоке концентрации пыли на рабочем месте превышали ПДК в 3,3 раза, у притока— в 7,4 раза; внутри камеры (за воздушной завесой)—в 13 раз, на выбросе—в 13,4 раза; в щели отсоса — в 121,6 раза. Однако при выключенном притоке эти концентрации резко падали и составляли на рабочем месте 2,7 мг/м3, т. е. были меньше ПДК почти в 2 раза, у притока воздух несколько загрязнялся за счет напыления и составлял 6,9 мг/м3, у воздушной завесы содержание пыли было таким же, как и на рабочем месте. При производительности распылителя 170—200 г/мин и полностью включенной вентиляции содержание пыли было значительным и превышало ПДК в среднем в 7,2 раза, а при увеличении производительности до 250 г/мин — в 36 раз, за воздушной завесой в камере — в 64,8, у притока — в 112,6 раз; в щели отсоса — в 171,6 раз; на выбросе — в 57 раз. При выключенном притоке эти концентрации также снизились до предельно допустимых и составляли на рабочем месте и у пульта камеры 5,6—5,7 мг/м3, в проеме камеры 6,9 мг/м3, в щели же отсоса концентрации остались аналогичными вышеописанным — 615 мг/м3, т. е. превышали ПДК в 123 раза. Пробы воздуха, отобранные без напыления (в обеденный перерыв), показали содержание пыли в пределах 3,2 мг/м3, а в конце рабочего дня — 7,2 мг/м3. Для снятия излишка порошка с изделий их обдували воздухом из шланга под давлением в 3 атм, при этом воздух загрязнялся пылью до 341,2 мг/м3, однако за счет отсоса воздуха в окрасочной камере эти концентрации падали через 3—20 мин до 11,2 мг/м3. В связи с этим отбор проб воздуха при напылении порошка на изделия проводился через 30 мин после сдува порошка.
Оплавление и сушка окрашенных деталей проводились в сушильном шкафу при температуре 200° С в течение 10— 30 мин. В дверце сушильного шкафа имелась небольшая щель (10 мм), у которой отбирались пробы воздуха на содержание формальдегида, ацетальдегида, метанола, диметилтерефталата. Результаты анализов представлены в табл. 28.
Таблица 28. Газовыделения при оплавлении порошковых покрытий
Из приведенных в табл. 28 данных видно, что выделение формальдегида в течение всего времени оплавления значительно, с превышением ПДК ДО 59 раз, хотя через 10 мин сушки его количество уменьшается почти вдвое. Концентрация ацетальдегида в первые 10 мин превышает ПДК в 1,7 раза, однако в последующие 10 мин она находится на уровне допустимой. Метанол выделяется в незначительном количестве, диметилтерефталат— с превышением ПДК более чем в 1000 раз.
Проведенные исследования на ручной венгерской установке в окрасочной камере показали, что воздушная среда как при напылении, так и при оплавлении загрязняется вредными веществами в концентрациях, значительно превышающих предельно допустимые. Эти концентрации особенно возрастают при увеличении производительности распылителя более 170 г/мин. Принципиальная схема вентиляции с подачей приточного воздуха сверху вниз и удалением загрязненного из нижней части камеры выбрана правильно. Положительным следует считать предусмотрение воздушной завесы для предотвращения выбывания вредных веществ из рабочего проема камеры.
Оборудование окрасочной установки рекуперационными устройствами позволяет очищать удаляемый воздух на 90% от пыли порошка и предотвращать загрязнение окружающей среды.
Несмотря на оригинальные и положительные моменты в проектировании общей схемы установки, состояние воздушной среды на рабочем месте является неудовлетворительным.
Фактические параметры движения воздуха на притоке через потолок, из приточного отверстия воздушной завесы, во всасывающем отверстии вытяжной щели не соответствуют паспортным данным. Они значительно ниже этих данных и распределение скоростей выхода приточного и удаленного из камеры воздуха неравномерно. Поступающий через потолок воздух плохо очищается в фильтрах, а также при рекуперации. В связи с этим в воздушную завесу поступает уже загрязненный воздух и она не только не выполняет своей основной функции, но и ухудшает состояние воздушной среды в зоне дыхания рабочего. Это подтверждается анализами воздуха. При выключении притока и воздушной завесы концентрации пыли на рабочем месте были на уровне ПДК.
Обеспечение благоприятных, безопасных условий труда на данной окрасочной установке возможно лишь при обеспечении равномерного выхода приточного воздуха в камере и равномерного всасывания загрязненного воздуха в вытяжном отверстии, предотвращении загрязнения — подаче чистого воздуха в воздушную завесу. Сушильный шкаф для оплавления и сушки изделий с порошковым покрытием следует оборудовать герметично закрывающимися дверками и вытяжной механической вентиляцией. Необходимо изменить технологию сдува порошка с окрашенных изделий.
С 1972 г. на Климовском машиностроительном заводе им. В. Н. Доенина эксплуатируется автоматическая линия по нанесению пневмоэлектростатическими распылительными установками поливинилбутираля на детали станков. Установка работает с системой рекуперации, состоящей из одного циклона, вытяжка осуществляется центробежным вентилятором. Производительность установки 160 г/м2. Нанесение порошкового покрытия осуществляется на изделия довольно сложной конфигурации. Режим отверждения проводится при температуре 150°С в течение 10— 15 мин.
Проведенные исследования содержания в воздушной среде на рабочем месте красочной пыли и вредных веществ показали, что их концентрации были в пределах допустимых и ниже. Для обеспечения благоприятных условий труда при нанесении порошковых покрытий ручными установками необходимо предусматривать выполнение определенных мер безопасности. Окраска должна проводиться в камерах, оборудованных механической вентиляцией. Окраска изделий вне камеры не допускается.
Для предотвращения выхода вредных выделений за пределы окрасочных камер в них должно поддерживаться разрежение. Скорость всасывания в рабочих проемах камер должна быть не менее 0,5 м/с.
Местные системы вытяжной вентиляции от камер следует оборудовать устройствами, предотвращающими загрязнение воздуховодов горючими отложениями и блокировками, обеспечивающими подачу порошка к распылителям только при включенных вентиляционных установках.
При организации механического притока воздух должен подаваться рассеянно в верхнюю зону с прохождением предварительной очистки через слой фильтрующего материала. Нижняя часть окрасочной камеры должна быть выполнена сужающейся в форме лотка. Удаление загрязненного воздуха следует осуществлять из нижней части камеры через щелевидное отверстие.
Для предотвращения образования вихревых потоков загрязненного воздуха в нижней части камеры и для обеспечения равномерности его удаления всасывающий воздуховод должен быть рассчитан как воздуховод равномерного всасывания. При разработке технологических процессов окраски следует предусматривать эффективную очистку воздуха перед выбросом в атмосферу (не менее 95%). Подачу порошковых полимерных красок к рабочему оборудованию необходимо блокировать с включением необходимых средств защиты.
Рабочие составы надо подавать централизованно из специальных краскоприготовительных отделений, оборудованных принудительной приточно-вытяжной вентиляцией. Для предотвращения выбивания порошковой пыли в воздух рабочего помещения ограждения окрасочных камер и узлы загрузки порошка в установках должны быть герметичными. Дверцы сушильных шкафов следует оборудовать герметичными прокладками. Для предотвращения выделения в воздух помещений вредных веществ при оплавлении и сушке порошковых покрытий сушильные камеры должны быть оборудованы механической вытяжной вентиляцией.
С целью исключения статической нагрузки на правую руку работающих следует предусмотреть устройство для механического поддерживания распылителя. Организация рабочего места при окраске должна отвечать эргономическим требованиям. На рабочем посту должно быть предусмотрено место для сидения.