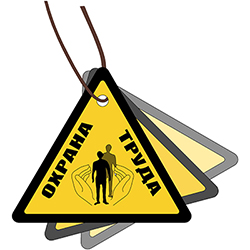
На ряде заводов 100—130-тонные типовые конвертеры 60-х годов были позже реконструированы на более тяжелую садку — до 160—170 т.
Продолжительность плавки в 165-тонном конвертере в среднем 45—55 мин, в зависимости от интенсивности дутья и организации труда. Продувка длится менее половины этого цикла. Остальное время расходуется на загрузку лома и заливку чугуна, ввод сыпучих материалов, пробы, выпуск плавки. В фурму подают обычно 3—3,5 м3 кислорода (99,5% 02) на тонну жидкой стали в минуту, под давлением 1,5—1,7 МПа.
Металлошихта состоит из мартеновского передельного жидкого чугуна (4—4,5% С; 0,7—0,8% Si; 0,8—1,2% Мп; 0,1% Р; не более 0,045% S) и малоуглеродистого лома в соотношении примерно 75 и 25%. Металлолом служит охладителем ванны. В процессе продувки он растворяется и расплавляется, отбирая часть тепла, выделяемого экзотермическими реакциями окисления части железа и его примесей. Этим ванна предохраняется от перегрева.
Быстрый ход конвертерной плавки и соответственно большая цикличность процесса позволяют обеспечить металлом высокопроизводительные обжимные, непрерывно-заготовочные и сортопрокатные станы; организовать равномерную их загрузку и рациональную эксплуатацию. Среднегодовая производительность 165-тонного конвертера достигает 130—135 т/ч. Работы по дальнейшему совершенствованию процесса ведутся в нескольких направлениях: повышается интенсивность продувки путем подачи 5—7 м3/(т*мин) кислорода через многосопловые фурмы; внедряется стандартизация шихтовых материалов для обеспечения стабильного режима плавки; строятся большегрузные конвертеры с садкой 350—400 т; разрабатываются автоматизированные системы управления технологическими процессами в цехе; развивается вне-печная обработка стали путем продувки ее в ковше инертными газами (аргоном и азотом) для уравнения температуры, химического состава и очищения стали от неметаллических включений.
«Ковшовая металлургия» специализирует конвертер на выполнение только интенсивного периода процесса — продувки ванны и освобождает его от относительно замедленной операции доводки стали. Вакуумирование стали в ковше применяется для более полной ее дегазации.
Перед технологами возникают новые задачи. Чтобы ускорить плавление металлолома, необходимо установить более жесткие требования к его физическому состоянию — размерам и насыпной массе; тщательно сортировать, пакетировать, смешивать тяжеловесный и легковесный лом. Надо отработать способ подвода кислородного дутья большого удельного расхода для ускорения шлакообразования, полного расплавления скрапа, при меньших потерях металла в выбросах из конвертера и меньших простоях его на замене фурм, добиться выхода годной стали в пределах 90—92%, усилить охлаждение тепловоспринимающих поверхностей газоотводящего тракта и кислородной фурмы, уменьшить заносы тракта плавильной пылью. Следует ускорить проведение вспомогательных операций и организовать работы участков в одном темпе с конвертерами.
Процесс плавки быстро набирает высокие скорости рафинирования ванны. Уже в первые 2—3 мин продувки окисляется практически весь кремний металлошихты, выделяя в реакционной зоне более 70% всего поступающего в это время тепла. Остальное тепло дают реакции окисления железа, марганца, углерода и первичного шлакообразования. Главным источником выделения химического тепла в плавке является реакция обезуглероживания. Углерода окисляется в 5—6 раз больше кремния. В общем балансе химического тепла на первом месте стоит углерод (55—60%), на втором — кремний (22—25%). На остальные реакции приходится 18—20%.
В начале продувки при пониженной температуре ванны (менее 1400°С) металлолом не плавится. Он насыщается углеродом из жидкого чугуна и растворяется в высокоуглеродистом расплаве при достижении температуры ликвидус (диффузионное плавление). Так растворяются, например, в жидкой стали тугоплавкие ферровольфрам и ферромолибден.
По мере нагревания ванны происходит собственно плавление лома. Оно заканчивается в конце продувки. Легковесная часть металлошихты, имеющая относительно большую поверхность контакта с расплавом, нагревается быстрее, чем пакетированный лом, полнее переходит (диффундирует) в металл, скорее его охлаждает. Однако использовать сплошь легковесный лом невыгодно, так как он удлиняет период загрузки его в конвертер.
Марганец и фосфор окисляются одновременно с кремнием и углеродом. Более сложен процесс обессеривания металла. Десульфурация (обессеривание) ванны от начальной концентрации 0,055—0,060% S до требуемого содержания 0,020—0,030% S достигается усиленной обработкой металла основным активным шлаком (CaO/Si02>2,5), но продувка и весь цикл плавки при этом затягиваются.
Известь задают в конвертер в начале продувки для возможно более раннего образования основного шлака, перевода большей части фосфора и серы из металла в шлак и удерживания их в шлаке в виде стойких соединений (СаОз, Р2О5 и CaS). Необходимо ускорить ассимиляцию извести шлаком. Задача затрудняется тем, Что период продувки продолжается недолго (в 165-тонном конвертере менее 20 мин) и имеет тенденцию к дальнейшему сокращению. Этого времени должно хватить не только на формирование шлака, но и на активное участие его в рафинировании ванны. Шлак в минимальной степени должен вспениваться, т. е. не задерживать выделяющиеся пузырьки СО, С02 и других газов.
Достаточная газопроницаемость шлака, его невспениваемость способствуют лучшему нагреванию ванны, равномерному протеканию обезуглероживания и равномерному выделению пузырьков газа по ее поверхности. Шлак меньше вспучивается, не доходит до горловины конвертера во время сильного перемешивания металло-шлаковой эмульсии. Устраняется одна из причин выбросов и выплесков жидких фаз. В этих случаях шлак легче отделяется от металла, а металл в меньшей степени налипает на фурму. Условия труда сталеваров улучшаются. Шлак участвует в снабжении ванны кислородом вторичным путем, через оксиды железа и марганца (FeO и МnО).
Главный источник газообразования в конвертерной плавке — реакция окисления углерода. Непосредственно над ванной (условной ее поверхностью) газовая фаза состоит из 88—92% СО и 8—12% С02 (в сухом объеме). Если в кессоне давление газа не регулируется (не поддерживается постоянным), то состав его в конвертере и в газоходе претерпевает существенные изменения. Происходит подсос атмосферного воздуха вследствие эжектирующего действия струи кислорода. В газовую фазу с кислородным дутьем, воздухом и из металлошихты поступает азот, туда же попадает плавильная пыль от испаряющихся в подструйной зоне железа, марганца и их оксидов и известковая пыль.
Большое количество тепла, выделяемого в окислительных реакциях, не может быть освоено конвертерной плавкой без ввода охладителя. Им служит главным образом стальной (железный) лом. Применение железной руды и известняка для этих целей менее оправдано ввиду затруднений с получением активного основного шлака и более частых выбросов из конвертера. Количество перерабатываемого в плавке лома определяется тепловым балансом процесса. Массу металлошихты рассчитывают так, чтобы поступление и поглощение тепла обеспечили необходимый нагрев ванны, а выход стали соответствовал количеству отливаемых слитков при минимальном остатке металла в ковше.
Тепловой режим конвертерной плавки имеет свои особенности. В начале продувки процесс идет при избытке охладителя, так как лом полностью загружается в конвертер до заливки чугуна. В этой стадии процесса надо скорее подогреть ванну, получить основной шлак и успеть использовать его для дефосфорации и десульфурации.
В первые минуты обескремнивания и поступления значительного количества тепла усиливается ассимиляция извести, растормаживается реакция обезуглероживания металла. При температуре порядка 1400°С и выше рафинирование ванны достигает максимальной скорости. Более раннему наступлению этого момента благоприятствует заливка в конвертер физически и химически горячего доменного чугуна (1330— 1350°С; 0,8—0,9%Si).
Перегруз металлолома сверх оптимального соотношения его с жидким чугуном приведет к увеличению продолжительности плавки. Кроме того, из-за относительно позднего образования основного шлака и задержки обезуглероживания возможен выброс из конвертера металла и шлака. В итоге снижаются и производительность конвертера, и выход годной стали.
Максимальное количество металлолома в шихте, которое позволяет нормально провести плавку на мартеновском передельном чугуне, составляет в среднем 270 кг на тонну стали. Вывод этот следует из теплового баланса конвертерной плавки с верхней продувкой.
Применение высококремнистого чугуна с содержанием более 0,8% кремния не увеличит энергетических ресурсов плавки и, следовательно, не даст возможности увеличить долю лома в плавке. Причина в том, что потребуется вводить больше извести в конвертер для нейтрализации повышенного содержания кремнезема в шлаке и сохранения оптимальной основности шлака. Увеличится его масса, возрастут потери тепла. Такая технология будет неэкономичной.
Проблема технологических выносов весьма существенна для конвертерного производства стали. С этим связаны заметные потери в плавке. Основную массу их составляют мелкие выносы: частицы размеров менее 0,1 мкм образуют дым, более крупные удаляются в виде плавильной пыли. Выносы состоят на 60—70% из железа, окислившегося над уровнем ванны. С плавильной пылью отходят также самые мелкие фракции извести, плавикового шпата и железной руды.
В ряде случаев выносы проявляются в опасной форме выбросов значительных масс металла, шлака (и газов) на рабочие места. Они причиняют ожоги сталеварам, нарушают ритмичную работу конвертеров, снижают выход годной стали, наносят материальный ущерб производству. Увеличивается запыленность и загазованность пролетов, загрязняются водоемы и воздушный бассейн местности.
Плавильная пыль и газы полностью не отводятся газовым трактом. Часть из них на выходе из горловины конвертера не попадает в подъемный газоход (юбку кессона) и остается в цехе. Количество выносимой с газами плавильной пыли составляет в среднем 150—200 г/м3. Механические потери металла в процессе продувки 165-тонной плавки доходят до 2,5—3 т.
Газопылевыделения начинаются во время заливки чугуна и загрузки первой порции сыпучих материалов. Над конвертером поднимается густой бурый дым, который доходит до перекрытия цеха и через аэрационный фонарь пробивается наружу. Бурый дым, возникающий в этот период плавки, обусловлен окислением в рабочей полости горячего конвертера мельчайших брызг заливаемого чугуна. Позже, в начале продувки, в дым переходят конденсирующиеся и окисляющиеся пары металлов.
Бурый дым не улавливается подъемным газоходом, так как при наливе чугуна горловина конвертера выступает за его пределы. Дымосос, сблокированный с механизмом наклона агрегата, отключается или переводится на пониженную нагрузку. Дым и газы собираются в верхней части здания и потом медленно оседают на рабочие места. По окончании заливки чугуна, когда горловину конвертера устанавливают под газоходом, дымосос снова включается на полную мощность.
Чтобы уменьшить количество мелких выносов из конвертера и оздоровить труд в цехе, рекомендуется:
1. Не завозить сыпучие шихтовые материалы (известь, плавиковый шпат, железную руду, окатыши) со значительным содержанием пылеватой фракции.
2. Рационально организовать дутьевой режим плавки: первые секунды работать при пониженном дутье и с максимально допустимым подъемом фурмы, чтобы меньше выдувать шихту из конвертера. Только с образованием первичного шлака увеличить подачу кислорода до нормальной интенсивности (ступенчатый режим дутья).
3. Улучшить конструкцию многосопловых фурм для достижения более спокойной продувки плавки. Отработать оптимальный режим рассредоточенного дутья.
4. Не заливать холодноватый (стылый) чугун, не перегружать садку охладителями, чтобы начать продувку с возможно меньшим окислением и испарением железа.
5. Держать горловину конвертера ровно под газоходом.
6. Для строящихся конвертеров проектировать газоотводящий тракт на максимальную пропускную способность.
Указанные явления с выносами материалов из плавки характерны для конвертеров с верхним дутьем. Выносы из конвертеров с донной кислородной продувкой будут значительно меньшими ввиду скрытого расположения реакционной зоны в объеме ванны.