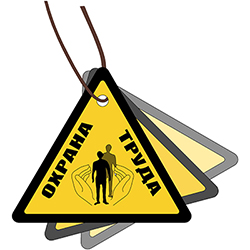
В качестве головной операции переработки свинцовых продуктов используется плавка на черновой свинец с последующим его пирометаллургическим рафинированием, что обеспечивает получение достаточно чистого от примесей металла и высокий процент извлечения свинца.
Но крупномасштабному внедрению пирометаллургических схем препятствуют экологические ограничения по пылеулавливанию и обезвреживанию отходящих газов. Получаемые продукты (шлаки, съемы, вторичные пыли) требуют доводки.
Нельзя сбрасывать со счетов проводимые исследования гидрометаллургических приемов при переработке вторичного неметаллизированного свинцового сырья. Общие недостатки этих методов — необходимость предварительной водной промывки кеков с образованием значительных количеств токсичных промышленных стоков; затруднение фильтрации пульп после отмывки, выщелачивания и других операций. Электроэкстракция свинца из загрязненных растворов приводит к образованию губчатых осадков, требующих дополнительного рафинирования; большинство гидрометаллургических операций со свинец содержащими растворами требует дополнительных затрат на безопасное обслуживание.
На кафедре металлургии тяжелых цветных металлов УГТУ-УПИ проведены исследования переработки свинцовых, свинцово-оловянных кеков по вариантам:
Так как в свинец содержащих кеках имеется значительные количества водорастворимых соединений, то головной операцией их гидрометаллургической переработки является отмывка. Это снижает содержание меди и цинка в кеке, а следовательно, и расход растворителя. При применении раствора этилендиамина (En) сульфат и оксид свинца растворяются в них согласно уравнению:
Для активного растворения оксида свинца необходимо присутствие в растворе серной кислоты или предварительная сульфатизация кеков. В течение 30 мин при температуре 293К в раствор извлекается до 95% свинца. Сульфидные соединения, благородные металлы, оксиды железа, висмута, олова и минералы пустой породы остаются в нерастворимом остатке. Низшие оксиды сурьмы и мышьяка частично переходят в раствор. Это требует применения кислотостойкого оборудования, ухудшает условия труда, увеличивает количество вредных стоков.
Результативным приемом выделения свинца из очищенных растворов этилендиамина является продувка их углекислым газом, что приводит к осаждению карбоната свинца, который после промывки и сушки пригоден для получения чистого оксида свинца, используемого при производстве хрусталя.
При выщелачивании кеков в растворах двунатриевой солиэтилендиаминтетрауксусной кислоты (ЭДТА) растворяются как сульфатная, так и оксидная формы свинца, т.е. можно обойтись без какой-либо предварительной подготовки свинец содержащих техногенных отходов. Характер изменения концентрации свинца в растворе по ходу выщелачивания свидетельствует о том, что скорость процесса со временем замедляется, она определяется плотностью пульпы. Конечное содержание свинца в растворе зависит только от концентрации ЭДТА («емкости» раствора по свинцу составляет около 40 г/дм3). Хорошие результаты достигаются при концентрации ЭДТА 140-150 г/дм3. При растворении сульфата и окиси свинца существует область нестабильных насыщенных растворов, где протекает обратная реакция:
Параллельно происходит кристаллизация трилонатного комплекса свинца, ассоциированного с сульфат-ионом.
Оптимальным способом выделения свинца из трилонатного раствора является электроэкстракция, позволяющая за одну операцию регенерировать растворитель и извлекать из него до 96% свинца. Основным недостатком прямого выщелачивания кеков является накопление в растворе ионов S042-, что негативно сказывается на показателях последующих операций. Вывод сульфат-иона в виде нерастворимого CaSО4 сопряжен с необходимостью выполнения дополнительных операций и получением гипсового продукта, осложняющего технологию. Поэтому целесообразно предварительной карбонизацией выводить серу из свинец содержащих отходов в концентрированных растворах карбоната натрия (калия):
Хорошие результаты карбонизации достигаются при концентрации Na2CО3 150 г/дм3 в течение часа. К преимуществам этого метода относится экологическая безопасность, и возможность использования аппаратуры из более доступных конструктивных марок стали.
Таким образом, среди отходов отработанных аккумуляторов могут встретиться железо, кадмий, никель, свинец, медь, мышьяк, перхлорвиниловая ткань (сепаратор, изолятор пластин электродов). В составе отработанного электролита щелочных аккумуляторов могут оказаться: едкий калий ГОСТ 9285-59 (КОН) с добавкой лития едкого ГОСТ 8595-83 (LiOH); едкий натр NaOH; сернистый натрий Na2Sx9H2О; борная кислота Н3ВО3. Электролитом автомобильных аккумуляторов является серная кислота H2SО4.
Все продукты в отработанных аккумуляторах представляют опасность для ОС и человека. Так, при хроническом воздействии едкого натра на организм человека наблюдается колликвационный некроз, а при поступлении внутрь организма - ожоги пищеварительного тракта, экзотоксический ожоговый шок, повторные желудочные кровотечения, механическая асфиксия в результате ожога и отека гортани, реактивный перитонит. В более поздние сроки (через месяц) — рубцовое сужение пищевода, астрального отдела желудка. Не менее опасным является кадмий.
Примером изучения возможности очистки от свинца сернокислых электролитов отработанных аккумуляторов является анализ ряда проб,взятых из отработанных электролитов. Анализу было подвергнуто 8 проб электролитов.
В соответствии с требованиями на электролит для аккумуляторных батарей (ГОСТ 667—73) разведенная свежая серная кислота для заливки в аккумуляторы должна иметь плотность 1,18 г/см3 (25% мас. = 300 г/л) для аккумуляторов открытого исполнения и 1,210 ± 0,005 г/см3 — для аккумуляторов закрытого исполнения; электролит из работающего аккумулятора соответственно должен иметь плотность 1,205 ± 0,005 г/см3 (28,5% мас. = 340 г/л) и 1,240 ± 0,005 г/см3(33% мас. = 405 г/л).
Содержание компонентов в пробах колеблется в пределах:
плотность, г/см3 - 1,045-1,265;
H2SO4, % мас. - 7,0-36,0 (70-457 г/л).
Содержание тяжелых металлов, мг/л:
Рb 2,1—9,5;
Сu 0,2-51,0;
As 0,06-0,15;
Fe 0,8-14,0;
Сумма: 3,16-74,65.
№ образца |
Плотность, г/см3 |
[H2S04],%. |
|
Содержание, мг/л
|
|
| ||
---|---|---|---|---|---|---|---|---|
плотн. |
титр. |
As |
Рb |
Сu |
Fe |
Сумма | ||
1 |
1,14 |
|
21,0 |
0,1 |
4,8 |
0,2
|
1,1 |
6,2 |
2 |
1,16 |
22,67 |
23,69 |
0,12 |
3,5 |
12,5
|
8,6 |
30,92 |
3 |
1,20 |
27,1 |
|
0,15 |
2,8 |
0,5
|
0,8 |
4,25 |
4 |
1,265 |
35,6 |
35,97 |
0,14 |
2,1 |
0,4
|
2,3 |
4,94 |
5 |
1,132 |
19,0 |
|
0,08 |
3,0 |
2,2
|
4,8 |
10,08 |
6 |
1,242 |
33,0 |
34,54 |
0,07 |
3,0 |
28,8
|
14,0 |
45,87 |
7 |
1,045 |
7,0 |
|
0,06 |
3,2 |
2,1
|
2,0 |
7,36 |
8 |
1,255 |
34,0 |
|
0,07 |
9,5 |
51,0
|
5,6 |
66,17 |
Допустимое содержание тяжелых металлов (мг/л) в разведенной кислоте для заливки в аккумуляторы и электролите из работающих аккумуляторов, рассчитанное в соответствии с требованиями ОКП 11 21.211.0730-09 на кислоту серную 1-го сорта ГОСТ 667-73, представлено в таблице.
Сопоставление данных таблиц позволяет увидеть, что в образцах проб 2, 6 и 8 отработанных электролитов наблюдается по сравнению с нормативными значениями превышение содержания меди, а содержание As, Рb и Fe находится в пределах нормативов.
Изучение возможности очистки электролита от соединений свинца их соосаждением с осадком сульфата бария доказало эффективность метода. В результате добавления к электролиту раствора соли бария выпадает осадок BaSO4, играющий роль коллектора и сорбирующий микроколичества PbSO4:
Тяжелый металл |
[H2S04], % маc.
| |||
---|---|---|---|---|
25,0 |
29,0 |
28,5 |
33,0 | |
As |
0,39 |
0,45 |
0,45 |
0,52 |
Рb |
49,2 |
57,177 |
56,1 |
64,9 |
Сu |
2,5 |
2,9 |
2,85 |
3,5 |
Fe |
49,2 |
57,1 |
56,1 |
64,9 |
Микропримесь |
Содержание, мг/л |
% очистки | |
---|---|---|---|
исходный |
декантат | ||
Рb |
2, |
0,03 |
98,6 |
Сu |
0,41 |
0,3 |
|
Fe |
2,3 |
2,3 |
|
As |
0,14 |
0,11 |
|
Достаточное для эффективного соосаждения свинца соотношение концентраций Ва2+ и Рb2+ составляет 100:1 и может быть уменьшено.
Результаты анализа декантата электролита 4 после введения в него раствора Ba(NO3)2 (соотношение концентраций Ва2+ и Рb2+ составляет 100:1) и отстаивания осадка в течение суток, представлены в таблице, из которой видно, что соосаждение Сu, Fe и As с осадком BaSО4 незначительно.
Образующийся осадок сульфата бария мелкодисперсный: он практически на 100 % проходит через фильтр «красная лента» (размер пор 3,5—10 мкм) и частично — через фильтр «синяя лента» (размер пор 1,0-2,5 мкм). Для отделения осадка может быть использовано фильтрование при пониженном давлении через стеклянные фильтры ПОР 1,0, ПОР 1,6 и ПОР 3 (ГОСТ 9775-69). Процесс седиментации и отстаивания осадка протекает в течение суток. Объем осветленной части электролита после его отстаивания составляет 90—95%.
Превышение нормативного содержания микропримесей в отработанных электролитах достигает 20-кратного (по меди). Содержание Pb, As, Fe находится в пределах допуска.
Очистка электролита от свинца может быть эффективно осуществлена его соосаждением с осадком сульфата бария при соотношении концентраций Ва2+ и Рb2+, равным 100:1; размеры частиц осадка BaSО4 не превышают 4-5 мкм; время отстаивания осадка — одни сутки. Соосаждение Сu, As, Fe с осадком BaSO4 незначительно.
Обезвреживание сернокислотных электролитов, в том числе и от соединений меди, может быть осуществлено путем их соосаждения с гидроксидом железа.
Непосредственно на производстве применяются разного рода установки регенерации кислот из отработанных травильных растворов.
Например, установка АО «Полимерсинтез» предназначена для получения регенерированной соляной кислоты концентрацией 20% мас. Из отработанных травильных растворов, содержащих травильную кислоту (HQ), хлористое железо (FeCl2, FeCl3), ПАВ (органические поверхностно-активные вещества), получают кислоту.
Основные технические характеристики установки:
— производительность 0,3 м3/ч;
— выход соляной кислоты не менее 90%;
— рабочая температура при ультрафильтрации и электрохимическом окислении не превышает 40°С;
— рабочая температура при гидролизе 165-170°С;
—занимаемая площадь 210 м3;
— высота 11 м.
Из ванны травления (1) отработанный травильный раствор через предварительный фильтр (2) подается на фильтрационный модуль (3), где под действием давления 0,3 МПа происходит удаление фракции ПАВ (II) из продуктов травления, которая может быть возвращена в ванну травления или утилизирована. Очищенный от органики раствор поступает в электролизер (4), в котором происходит электрохимическое окисление двухвалентного железа в трехвалентное. Полученный раствор концентрируется в испарителе (5) путем отгона избытка воды (сюда же подается пар) и направляется в реактор-гидролизер (6), в котором на первом этапе происходит дальнейшее концентрирование хлорного железа за счет отгона свободной соляной кислоты (концентрацией до 20% мас.) в сборную емкость (9) через теплообменник (8).
Сконденсированный охлажденный продукт (соляная кислота) может быть возвращен в основное производство (в ванну травления). Оставшийся в реакторе (6) продукт подвергается гидролизу под воздействием воды, отогнанной из испарителя (5) и сконденсированной в теплообменнике (7). Образующийся хлористый водород отводится из системы вместе с парами воды, не занятой в реакции гидролиза (10). Сухой остаток после гидролиза (12), содержащий, в основном, окислы железа, отправляются на утилизацию.<