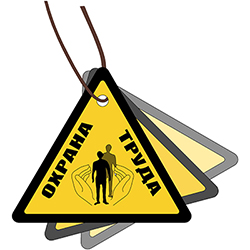
Источниками загрязнения ОС являются металлургические, химические и машиностроительные производства, предприятия нефтехимии, строительной индустрии и другие, связанные с дроблением и измельчением материалов, перегрузкой и транспортировкой сыпучих веществ. Необходимо отметить, что химическая и биологическая активность пыли несравненно выше, чем у исходных материалов, так как некоторые вещества в аэродисперсном состоянии приобретают, новые свойства (например, каменноугольная пыль и пыль некоторых органических веществ взрывоопасны).
Наибольший и наименьший размеры частиц пыли характеризуют диапазон дисперсности данной пыли. Основная масса пыли, образующейся в результате механического измельчения, состоит из частиц размером 5-50 мкм. Твердые частицы, образующиеся при химическом взаимодействии газов, обычно имеют размер менее 3 мкм, а пыль после сгорания угля — 5—70 мкм.
Способы борьбы с загрязнением атмосферы основаны на усовершенствовании технологических процессов (работа по замкнутому циклу, безотходные технологии), снижении до минимума количества отходов комплексным использованием сырья (на нефтехимических и металлургических предприятиях сооружают сернокислотные цеха, используя выбрасываемый сернистый ангидрид), внедрении прогрессивных методов горения (бездымное тушение кокса), использовании для газообразных выбросов высоких дымовых труб, чтобы снизить концентрацию вредных веществ у поверхности земли.
Но использование высоких труб приводит к загрязнению удаленных районов. Коренное решение этого вопроса заключается! в эффективной очистке от вредных газов и пыли до их выброса в атмосферу. В зависимости от дисперсного состава пыли, влажности и других факторов применяют соответствующий тип пылеуловителя. При этом основным критерием является степень очистки и экономические затраты (стоимость оборудования, монтажа, потребной электроэнергии, эксплуатационных и амортизационных расходов).
Хотя имеет место многообразие конструкций пылеуловителей, все они основаны на принципах осаждения взвешенной фазы. Пылегазовые смеси представляют собой аэродисперсную систему, в которой дисперсная фаза (пылинки) распределены в дисперсионной среде (газе). Движущими силами процесса осаждения пыли являются: сила тяжести частиц и сила диффузии частиц вследствие броуновского движения. Гравитационным полем (силой тяжести) осаждаются только относительно крупные частицы пыли.
Поэтому пылеуловители базируются на использовании силового поля, которое необходимо создать искусственно (силы инерции при изменении направления и скорости пылегазового потока; электрического притяжения заряженных частиц к осадительному электроду; процесс коагуляции — образование элемента из нескольких частиц; фильтрование газа через пористые перегородки). Чтобы не допустить обратного процесса, мешающего пылеулавливанию (возвращение осевших частиц обратно в поток газа); принимаются специальные меры: смачивание осадительной поверхности, снижение скорости потока, повышение его влажности.
Все эти принципы осаждения достаточно подробно рассмотрены в других главах данной книги.
Серьезной проблемой современности являются значительные выбросы сернистого ангидрида и окислов азота, которые разносятся на огромные расстояния и выпадают в виде «кислотных дождей», заражая водоемы, зеленые насаждения, грунтовые воды. Выбросы этих вредных веществ наблюдаются в металлургии, при производстве серной кислоты и минеральных удобрений.
Наиболее перспективным направлением развития сернокислотного производства считают получение кислоты по схеме ДКДА (двойное контактирование — двойная абсорбция). Общая степень контактирования в процессе достигает 99,8%, дополнительной очистки газа от сернистого ангидрида не требуется, выбросы SО2 в атмосферу в два-три раза ниже, чем при одностадийном контактировании; повышается коэффициент использования сырья.
Крупная сернокислотная система эксплуатируется на Череповецком ПО «Аммофос», оснащенном печами КС-450 с водотрубными котлами-утилизаторами, системой сухой газоочистки, с помощью сухих электрофильтров. Улавливание тумана и брызг серной кислоты осуществляется в волокнистых брызгоуловителях.
Из безотходных способов получения минеральных удобрений заслуживает внимания производство нитрофосфатов в Норвегии: фосфатное сырье разлагают 60% азотной кислотой при температуре 50-55'С в течение 2 ч. Нитрат кальция удаляют охлаждением при температуре -5°С в кристаллизаторах, охлаждаемых аммиаком. Фильтрация нитрата кальция производится в каскадных барабанных фильтрах с переводом его в нитрат аммония и карбонат кальция. После удаления нитрата кальция раствор нейтрализуется аммиаком, упаривается и гранулируется с калийными солями.
Основными отходами производства серной кислоты и минеральных удобрений являются отходящие газы, содержащие двуокись серы, фтористые соединения, аммиак, окислы азота и твердые отходы: пиритный огарок и фосфогипс.
При сгорании топлива в ТЭЦ в выбросах наблюдается значительное количество окислов серы и азота.
Основными методами очистки являются:
Существуют способы очистки топочных газов с получением минеральных удобрений: к газовому потоку добавляется озон, олефин и водяной пар. При взаимодействии этих трех добавок между собой получается азотная и серная кислоты, а взбрызгивание аммиака приводит к образованию сульфатов и нитратов аммония. Аналогичные технологии получения минеральных удобрений применены во многих странах мира.
На симпозиуме в г. Эссен (ФРГ, 10-11 ноября 1983 г.) отмечалось, что во Франции за 1971-1981 гг. эмиссия SО2 снизилась на 20%, в Англии — на 40%, что пошло на производство строительного гипса и минеральных удобрений. В Японии по состоянию на 1.01.95 г. эксплуатировалось 1366 единиц оборудования для улавливания из дымовых газов S02 общей мощностью 128х106м3/ч и 188 единиц оборудования — для улавливания NОX общей мощностью 72х106м3/ч.
Отходящие серосодержащие газы сернокислого производства очищаются аммиачно-сульфатным, азотно-каталитическим, кислотно-каталитическим или аммиачно-циклическим методом. Аммиачно-сульфатный метод заключается в абсорбции диоксида серы раствором сульфита и бисульфита аммония с последующим разложением этого раствора серной кислотой. Выделяющийся при этом диоксид, серы направляется на сжижение или в основное сернокислое производство.
Образующийся раствор сульфата аммония перерабатывается в сухой продукт или: используется при производстве минеральных удобрений. Метод обеспечивает надежную очистку отходящих газов до требований санитарных норм. К недостаткам метода можно отнести необходимость затраты серной кислоты на разложение сульфит-бисульфитных растворов, аммиака и переработки сульфата аммония.
В аммиачно-циклическом процессе в раствор, выводимый с установки улавливания газов, добавляют аммиак: часть полученного раствора (при содержании бисульфита аммония 820 г/л) подают в отгонную колонну для получения 100% SО2, а остальное — выводится как товарный продукт.
При производстве экстракционной фосфорной кислоты и минеральных удобрений из фтористых соединений производится извлечение фтористых соединений из технологических газов. В производстве простого суперфосфата отходящие газы промывают водой в механических камерах с разбрызгивающими валками и с последующим доулавливанием в полой башне. Недостатком метода является налипание на вращающиеся части кремнегеля. Другим вариантом процесса извлечения фтора из газов при производстве суперфосфата является абсорбция в трубе Вентури в две ступени, но при этом происходит засорение и быстрый износ форсуночных устройств, что приводит к ухудшению степени очистки газа.
В Японии для очистки отходящих газов производства суперфосфата и экстракционной фосфорной кислоты от фтористых соединений применяют водно-щелочную абсорбцию (2% раствор NaOH). Процесс протекает в двух последовательно установленных колонках. Фтористые соединения выводятся в виде фтор силикатов. Из-за высокого значения рН абсорбционного раствора не происходит забивание колонок, достигается высокая степень очистки отходящих газов.
При производстве экстракционной фосфорной кислоты на 1 т Р2О5 приходится 4,5 т фосфогипса, имеющего в своем составе нежелательные примеси (уран, асбест, тяжелые металлы). Этот процесс используют в странах, не имеющих богатых месторождений природного гипса; другие страны перерабатывают фосфогипс на гипсовые вяжущие. Например, в ФРГ по такому пути получают а-полугидрат после флотации и обезвоживания (в автоклаве при температуре 120°С и рН 1-3) фосфогипса, а в Ирландии — порошкообразного вяжущего для производства сухой штукатурки.
В число вариантов переработки фосфогипса на вяжущие входят его очистка от примесей, сушка, частичная дегидратирование до полугидрата, гранулирование, обжиг и размалывание. После этого продукт используют для получения строительного гипса. В США для нейтрализации фосфогипса используется аммиак (вместо извести, карбонатов кальция и натрия), что улучшает качество получаемой штукатурки. В Японии фосфогипс без предварительной обработки перерабатывают на добавки к цементу, используют при производстве гипсокартонных плит, перегородок и облицовочных материалов. Во Франции, Австрии, Финляндии и Бразилии разработана технологическая схема производства β-полугидрата: фосфогипс очищается от примесей флотацией или гидроциклонированием, после чего производят обжиг.