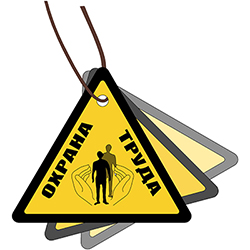
Весь опыт борьбы с загрязнениями окружающей среды демонстрирует необходимость введения безотходных или малоотходных производств и технологий. Термины «безотходная технология» или «малоотходная; технология» понятия: в какой-то мере относительные, так как абсолютно безотходных технологий не существует. Но этот термин характеризует степень совершенства примененных данном производстве, технологических, процессов и схем, обеспечивающих предел наиболее, полного использования сырья и энергии.
Основными путями защиты ОС от загрязнений является уменьшение объема промышленных сточных вод и разработка новых надежных способов их очистки. Этого можно достичь при повторном или многократном использовании очищенных сточных вод. Степень такой очистки регламентируется только технологическими требованиями.
Количество промышленных стоков можно значительно уменьшить изменением технологии производства некоторых синтетических смол (применением азеотропного метода синтеза при получении алкидных смол вместо блочного; использованием в производстве фенолоформальдегидных и карбамидных смол параформа вместо формалина; применением в качестве охлаждающего агента вместо воды — воздуха).
В 80-е годы XX столетия были разработаны сотни типов лазерной техники мощностью 1—5 кВт (типа «Квант», СО2-лазеры), продемонстрировавших высокую эффективность лазерных технологий. В настоящее время нашли широкое применение в машиностроении и для обработки материалов лазеры мощностью в 10 кВт, работающие в составе лазерных технологических комплексов при обеспечении выпуска продукции малыми сериями. Лазерная техника позволила внедрить широкий круг технологических процессов обработки самых разных материалов.
Например, лазерная резка легированных сталей и цветных металлов толщиной в несколько сантиметров при сложном профиле резки ведется при высокой производительности (до 10 м/с) и отличном качестве. Большую точность (т.е. минимальные отходы) при использовании лазерных технологий можно обеспечить при изготовлении мебели, художественного паркета, сувениров; Но особенно перспективно применение лазеров при резке трудно обрабатываемых материалов: керамики, пластика, стекла, базальтовых.
Лазерная сварка обеспечивает: минимальные остаточные деформации, что: особенно важно при производстве ряда ответственных деталей (трансмиссий, инструментов); высокое качество шва (ответственные продуктопроводы высокого давления, корпуса оборудования); огромную производительность (банки для консервирования, аэрозольные баллоны); уменьшение вредных выбросов.
Использование лазерных технологий позволяет многократно повысить качество и производительность перфорирования отверстий при изготовлении шумопоглощающих экранов, сит, фильтров, систем распыления жидкостей и газов, обеспечивает высокую экологическую чистоту.
Не менее важной задачей является сохранение здоровья населения. Это требует от пищевой промышленности обеспечить выпуск продукции, не допускающей вредных включений; особенно микроорганизмов. Для уничтожения вредных микроорганизмов используют: стерилизацию, внесение химических консервантов, замораживание. Но некоторые продукты стерилизовать нельзя, так как уничтожаются и обеспечивающий их качество вид микроорганизмов (например, кисломолочные продукты), химические консерванты вредны для здоровья, а в замороженных продуктах некоторые микроорганизмы остаются жизнеспособными.
Поэтому необходимо перекрыть доступ их в конечный (готовый, консервированный) продукт. Поскольку основным источником загрязнения его является воздух помещения (на каждые 1000 взвешенных частиц в воздухе приходится один микроорганизм), персонал, оборудование и сырые продукты, чистая технология должна обеспечить гарантированную чистоту воздушной среды в помещении, а, следовательно, длительное хранение продуктов питания и новый подход к консервированию. Такая технология должна обеспечить переработку продукта в его критической стадии в условиях чистого воздуха при минимальном применении химических средств.
Примером применения современной технологии является промышленное производство интегральных схем и элементов компьютерной техники. Переход к производству интегральных схем в промышленных масштабах на основе поликристаллического кремния и необходимость обеспечения высочайших требований к чистоте самого кремния как исходного материала привела к использованию бестигельной зонной плавки.
Для обеспечения промышленных объемов выпуска поликремния необходимой чистоты при наличии токсичности исходного сырья (SiHCl3 и других побочных продуктов технологического процесса (различные хлорсиланы, хлориды кремния, хлористый водород) требуется применение современных технологий, исключающих вероятность выбросов токсических продуктов в окружающую среду, особенно загрязнение воздушного и водного бассейнов.
Примером малоотходной технологии получения поликремния может служить химическая рециркуляция первичных реагентов. Такая технология позволяет практически полностью превратить все перерабатываемое исходное сырье даже при наличии термодинамических ограничений. Технологический процесс обеспечивает максимальную производительность единицы реакционного объема путем увеличения плотности подачи исходного сырья в реактор.
Важнейшим этапом технологического процесса производства пол и кристаллического кремния является выделение смеси хлорсиланов из образующейся парогазовой смеси (например, с использованием криогенной конденсации). На следующих этапах производится разделение смеси хлорсиланов на составляющие их индивидуальные вещества с помощью ректификационных колонок. Входящие в состав смеси водород и хлористый водород разделяются на установках криогенной фракционной конденсации. На процесс получения поли кристаллического кремния, основанного на обратимой химической реакции, восстановления водородом трихлорсилана (ТХС) SiHCl3 или тетрахлорида кремния (ТК) SiCl4, накладывается ряд ограничений, определяемых термодинамикой и кинетикой.
Термодинамические ограничения связаны с недостаточной степенью превращения хлорсиданов даже при достижения термодинамического равновесия. При этом избыток водорода не может превышать шестикратной величины при резком ухудшении структуры и поверхности получаемых кремниевых стержней. Кинетические ограничения определяются, тем, что при одноступенном протекании процесса желание получить максимально возможное извлечение приводит к резкому снижению скорости осаждения кремния.
Переход на рециркуляционный процесс получения поликристаллического кремния восстановлением хлорсиданов водородом дает возможность полностью освободиться от рассмотренных выше термодинамических и кинетических ограничений. Такой процесс становится экономически оправданным, обеспечивает максимальную скорость осаждения кремния без снижения общего извлечения.
К тому же рециркуляционная технология получения поликристаллического кремния кроме полной переработки исходных хлорсиданов позволяет повторно использовать непрореагировавший водород и образовавшийся хлористый водород, что не допускает загрязнения окружающей среды высокотоксичными продуктами реакции. Применение этой технологии кроме указанных достоинств (экономических и экологических) обеспечивает высокое качество продукции (получение поликристаллических кремниевых стержней правильной геометрической формы с мелкозернистой структурой и гладкой поверхностью).
Блок-схема установки для получения поликристаллического кремния из трихлорсилана представлена на рис. 8.1.
Чтобы понять механику функционирования данного малоотходного процесса получения кремния можно представить эту схему в несколько развернутом виде: в.виде ступенчатого осуществления процесса разделения компонентов с выводом продуктов реакции на каждой ступени (рис. 8.2).
Как можно видеть на рис. 8.2 в каждую последующую ступень технологического процесса поступает не прореагировавшее в предыдущей ступени сырье. При этом каждый цикл рециркуляции описывается выражением (1):
где Р — степень превращения в одной (каждой) ступени; Рс — суммарная степень превращения (во всех ступенях); а — доля рециркулята от общего количества компонента на входе в реактор.
Рис. 8.1. Блок-схема установки для получения кремния:
Мв — количество компонента, выводимого из системы; М — количество компонента на входе в реактор; Мк — количество компонента на входе в систему; Мр — количество рециркулята, Мп — количество компонента на подпитку