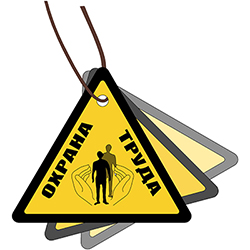
Таким образом, если в первую ступень процесса поступает Мп единиц исходного сырья, то на выходе из нее получается (1-а) долей продукта (химического превращения) и а долей химически измененного сырья. Следовательно, во вторую ступень поступает а х Мп единиц сырья, а выдается (1—а) х а х Мп продуктов превращения и а2 Мп не прореагировавшего сырья. В итоге на п-ю ступень поступает а(п-1) х Мп единиц сырья и с нее выдается (1-а) х а(п-1) х Ма продуктов реакции.
Рис. 8.2. Представление рециркулярного процесса в виде единичных (по ступеням) процессов
Суммарный расход компонентов сырья Мс во всех последовательно соединенных ступенях технологического процесса составит
В выражении (2) каждый член геометрической прогрессии определяет последовательность возвращения не прореагировавшего сырья на данный момент времени в соответствующую ступень установки.
Так как всегда а < 1, то при числе ступеней, стремящемся к бесконечности, величина, ап как угодно близко приближается к нулю, т.е. выражение (2) с учетом (1) примет вид (3):
Из выражения (3) можно получить формулу (4) для определения коэффициента рециркуляции:
Если режим работы системы устоялся, то с помощью коэффициента рециркуляции можно определить как суммарный расход компонента (поступающего на подпитку и рециркулята) на входе, так и суммарный выход целевого продукта.
Определение коэффициента рециркуляции можно выполнить по любому компоненту реакции (целесообразно по целевому продукту). Пусть целевым продуктом является вещество б. Тогда, обозначив его долю от суммарного расхода компонентов реакции процесса на входе реактора через Д а от расхода на подпитку свежим сырьем через Рд, можно получить выражение для определения общего количества полученного вещества б:
Если разделить обе части выражения (5) на Мп, то получится
а поэтому
Принципиальная схема рециркулярного процесса получения пол и кристаллического кремния восстановлением трихлорсилана (ТХС) и тетрахлорида кремния (ТК) водородом представлена на рис. 8.3 и 8.4.
При восстановлении ТХС водородом в установившемся состоянии для случая возврата в процесс заданных количеств ТК можно записать:
где М (ТХС) и М (ТК) — количество ТХС и ТК на входе реактора; Мп (ТХС) — расход материала, поступающего на подпитку; Мр (ТХС) и Мр (ТК) — количество веществ, возвращающихся в процесс при рециркуляции.
В данном случае количество ТХС-рециркулянта равно общему количеству ТХС, попавшего в реактор, с учетом убыли ТХС на получение конечного продукта (кремния) и ТК, а также на потери при конденсации:
где р — степень превращения в одной (каждой) ступени процесса; у — доля ТХС, перешедшая в ТК; ск— степень конденсации ТХС в конденсаторе.
Потерями ТК при конденсации можно пренебречь, так как упругость его пара значительно ниже, чем у ТХС. Это дает возможность из выражения (8) получить:
где ср — доля ТК, выводимая из куба ректификационной разделительной колонны;
Из выражений (10) и (12) следует:
Здесь выражение К (о6щ)= [М(тхс)+М(тк)]/Мп(тхс) является суммарным коэффициентом рециркуляции, учитывающим возврат части ТК в рецикл, а Кр(тхс) =(Мп+Мр)тхс/Мп(тхс) — коэффициентом рециркуляции ТХС.
Рис. 8.3. Принципиальная схема восстановления трихлорсилана (ТХС) водородом
Рис. 8.4. Принципиальная схема восстановления тетрахлорида кремния (ТК) водородом
Из слагаемого выражения (16) Кр(тхс) х ск х(1— р—у) видно, что суммарное извлечение продукта тем значительнее, чем больше коэффициент рециркуляции Кр и степень конденсации Ск, а также чем меньше доля ТХС (у), превратившегося в ТК. А слагаемое Кр(тхс) х у х(1-ср)/ ср указывает, что обеспечение возвращения части ТГК в рецикл также повышает суммарное извлечение продукта. Но возвращение ТК в рецикл приводит, к ухудшению энергетических и кинетических характеристик процесса (снижается скорость осаждения, уменьшается извлечение продукта за один цикл, увеличиваются энергозатраты). Поэтому осуществлять возвращение ТК в рецикл можно рекомендовать лишь для обеспечения минимальных расходов исходного сырья (ТХС).
В этом случае суммарное извлечение определяются преимущественно долей ТХС, перешедшей в ТК, величиной однократного превращения и степенью конденсации ТХС. На рис. 8.4 приведена схема рециркуляционного процесса получения кремния при восстановлении: ТК водородом, которая экономически целесообразна лишь в случае, если весь ТХС, образующийся на первой стадии восстановления (SiCI4+H2 = SiHCl3+НСl) и не прореагировавший в реакторе ТК полностью возвращаются в рецикл. Уравнение материального баланса для такого случая имеет вид:
или после соответствующих преобразований:
где х — доля ТК, превратившегося в ТХС.
Но так как (Мп(тк)+Мр(тк))/Мп(тк) = Кр(тк), то выражение (19) примет вид:
А так как (Мп(тк)+Мр(тк))/Мп(тк) = Кр (общ) = рс/р, то:
Из уравнения (21) можно сделать некоторые выводы.
1. Величина Кр(тк)х Х хск(1-р)/[1-скх(1-р)], определяющая полноту возврата образовавшегося ТХС в рецикл и эффективность процесса восстановления ТК водородом в целом тем больше, чем значительнее величина коэффициента рециркуляции ТК, степень превращения ТК в ТХС и коэффициент конденсации ТХС.
2. Слагаемое Кр(тк) х (1-х) х (1-ср), характеризующее количество возвращаемого ТК, указывает, что чем полнее обеспечен возврат в рецикл не прореагировавшего ТК, тем значительнее суммарное извлечение кремния.
Воздействовать на величину однократного извлечения (р) и коэффициента перехода (у) ТХС в ТК при установившихся параметрах технологического процесса восстановления (температура, мольное отношение Н2/ТХС, плотность подачи ТХС в аппаратуру восстановления) можно лишь в незначительной степени. Это определяется ограничениями, накладываемыми термодинамикой и кинетикой при установившихся параметрах процесса. Но, тем не менее, можно управлять полнотой конденсации ТХС для обеспечения его возврата в процесс, что окажет существенное влияние на величину суммарного извлечения кремния в рециркуляционном процессе.
На практике в установившемся режиме можно получить значения р = 0,2 и у = 0,25. Тогда выражение (17) примет вид:
Рс= р/[1-скх(1-р-у)] = 0,2/скх[1-0,2х(1-0,2-0,25)] = 0,2/(1-0,55 ск).
Теперь, подставляя соответствующие значения коэффициентов конденсации (ск), можно проследить изменение степени суммарного извлечения продукта (рс). Из анализа полученных данных примера можно сделать вывод, что увеличение коэффициента конденсации (ск) приводит к повышению суммарного извлечения кремния, т.е. целесообразно в процессе поддерживать максимально возможную полноту конденсации ТХС. Но так как 100% конденсации достигнуть невозможно, то в рассмотренном технологическом режиме принимается величина ск = 0,95—0,99. Как можно видеть из изложенного, в данном малоотходном процессе получения поликристаллического кремния значительная роль отведена водороду. Количество водорода на входе в реактор можно описать выражением
а сам процесс регенерации водорода
где д — доля водорода, принявшего участие в обеспечении протекания реакций (SiCI4+H2= SiHCI3+HCl; SiCl2+H2 = SiH2Cl2); кв — доля водорода, выводимого из рециркуляции,по мере накопления примесей.
Отсюда можно определить коэффициент рециркуляции водорода Кр(н)= [1-(1-д)х(1-кв)]-1.
Для получения и регенерации водорода из отходящей парогазовой смеси (ПГС) в данном процессе более целесообразно применять криогенную технологию, которая обеспечивает кроме регенераций водорода регенерацию как не прореагировавшего ТХС, так и продуктов реакций (дихлорсилана, хлористого водорода). Эта технология обеспечивает более низкие энергозатраты. Целесообразно применять в криогенной технологии многоступенчатую фракционную конденсацию хлорсиланов с вымораживанием хлористого водорода из ПГС и возвратом освобожденного от примесей водорода в реактор.
Криогенная технология обеспечивает:
Сущность криогенной технологии регенерации водорода в рассматриваемом процессе заключается в том, что отводящаяся из восстановительной системы ПГС после компримирования последовательно проходит ряд теплообменников, в которых противотоком движутся потоки охлажденных газов (водорода и хладоносителя — азота).
На последней ступени движения потока происходит вымораживание хлористого водорода при температуре порядка —190°С. При этом охлажденный водород и газообразный азот (—140°С) обратными потоками возвращаются в систему, где происходит конденсация хлорсиланов. В качестве промежуточного хладагента применяют фреон с температурой —(55—60)°С.
Присутствующие в ПГС хлорсиланы полностью конденсируются в области температур —(100—120)°С, а содержание хлористого водорода в этом диапазоне температур остается в ПГС без изменения. На этом принципе основано выделение или вымораживание конкретных компонентов, входящих в состав ПГС. Таким образом, по мере конденсации высококипящих хлорсиланов, ПГС обогащается легкокипящими компонентами (так, при температуре —60°С тетрахлорсилан в ПГС практически отсутствует, а концентрация ТХС в газовой фазе достигает 85%).
Сам процесс содержит 4 стадии охлаждения ПГС:
Рассмотренная малоотходная технология нашла достаточно широкое применение в промышленности.