Методы контроля при герметизации
Безопасность эксплуатации герметичных систем, находящихся под давлением
Безопасность эксплуатации герметичных систем, находящихся под давлением
На рис. 83 представлена схема фотографического метода просвечивания, который является одним из основных видов обнаружения дефектов рентгеновскими и гамма-лучами.
Как видно из схемы, пучок рентгеновских или гамма-лучей, пройдя через контролируемый элемент 2, действует на фотопленку 5, находящуюся в светонепроницаемой кассете 5. Для предохранения фотопленки от действия вторичных лучей за кассетой помещен свинцовый экран 4.
Рентгеновские или гамма-лучи, проходя через контролируемый элемент на участке, имеющем поры или трещины, будут меньше поглощаться, чем в соседних плотных, бездефектных участках. Дефекты будут отмечены на пленке более сильным ее потемнением. Основные достоинства рентгено- и гаммадефектоскопии: возможность получить наглядное представление о характере пороков и их протяженности; высокая чувствительность, позволяющая выявлять мелкие трещины; широкий диапазон контролируемых толщин (от 3 до 250 мм, а при использовании бетатрона до 500 мм и более).
Основные недостатки: низкая производительность; опасность для обслуживающего персонала, большое число факторов, влияющих на чувствительность.
Механическим испытаниям должны подвергаться стыковые сварные соединения с целью проверки соответствия их прочностных и пластических характеристик требованиям технических условий на изготовление.
К основным обязательным видам механических испытаний относятся:
1) статические испытания на растяжение и изгиб для определения предела прочности и пластичности металла;
2) динамические испытания на ударную вязкость.
Из каждого контрольного стыкового сварного соединения вырезаются по два образца для испытаний на статическое растяжение и статический изгиб или сплющивание и три образца для испытаний на ударную вязкость. В ряде случаев некоторые испытания можно не проводить; например, испытание на статическое растяжение не является обязательным для кольцевых сварных соединений сосудов цилиндрической формы и для труб при условии 10%-ного контроля этих соединений ультразвуковой дефектоскопией или просвечиванием.
Показатели механических свойств сварных соединений должны определяться как среднеарифметическое значение результатов испытаний отдельных образцов. Общий результат испытаний считается неудовлетворительным, если хотя бы один из образцов по любому виду испытаний показал результат, отличающийся от установленных норм в сторону снижения более чем на 100%. Например, значение ударной вязкости металла шва должно быть не ниже значений, определяемых табл. 21.
Таблица 21. Минимальное значение ударной вязкости шва, кгс • м/см
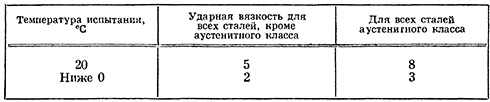
Металлографические исследования сварных швов и соединений сводятся к изучению макро- и микроструктуры и исследованию структуры металла по излому. При металлографических исследованиях изучают макроскопическую и микроскопическую структуру швов.
Макроскопические исследования (исследования макрошлифов) проводят невооруженным глазом или при очень малых увеличениях (не превышающих 20-кратное). Они позволяют выявить характер первичной кристаллизации металла шва, глубину и форму провара, ширину и очертания зоны термического воздействия, возможные пороки в виде непроваров, макротрещин, пор и шлаковых включений, неоднородность структуры шва, размеры зерен в наплавленном и основном металлах.
Микроскопические исследования проводят на шлифах с помощью микроскопа. Этот вид исследования дает возможность изучить более тонкие структуры шва и тем самым лучше выявить особенности и дефекты сварного соединения (например, микроскопические дефекты в виде пор, трещин и т. д.).
Гидравлическим испытаниям подлежит большинство из рассмотренных выше устройств и установок. При гидравлических испытаниях проверяются герметичность и прочность испытуемого объекта.
Гидравлическое испытание сосудов и их элементов должно производиться пробным давлением в соответствии с данными табл. 22.
Таблица 22. Давление при гидравлических испытаниях
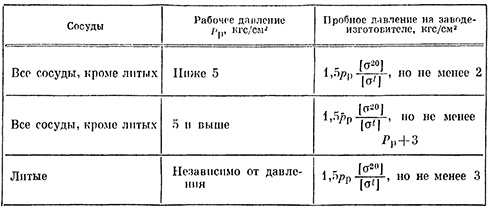
В табл. 22 [σ20] и [σt] — допускаемые напряжения для материала сосуда или его элементов соответственно при температуре стенки 20° С и расчетной температуре t стенки, кгс/см2.
Отношение [σ20]/[σt] есть наименьшее из отношении, взятых для всех
материалов, из которых изготовляются элементы сосуда. Величина пробного давления для сосудов и их элементов, работающих под давлением при минусовых температурах, принимается такой же, как при температуре 20° С.
В соответствии с табл. 22 производится также гидравлическое испытание сосудов при периодическом техническом освидетельствовании. При этом для сосудов, работающих при температуре стенки от 200 до 400° С, величина пробного давления не должна превышать рабочее давление более чем в 1,5 раза, а при температуре стенки выше 400° С — более чем в 2 раза. Для сосудов, изготовленных до 1 апреля 1974 г., допускается проведение гидравлического испытания тем же пробным давлением, что и на заводе-изготовителе.
Воздухопроводы, газопроводы инертных газов и ряд других трубопроводов подвергают гидравлическим испытаниям при давлении 1,25 рр (но не менее 2 кгс/см2), которое выдерживается в течение 5 мин.
Для гидравлических испытаний устройств и установок обычно применяют воду с регламентированной температурой. Измерение давления производят двумя манометрами, один из которых обязательно контрольный.
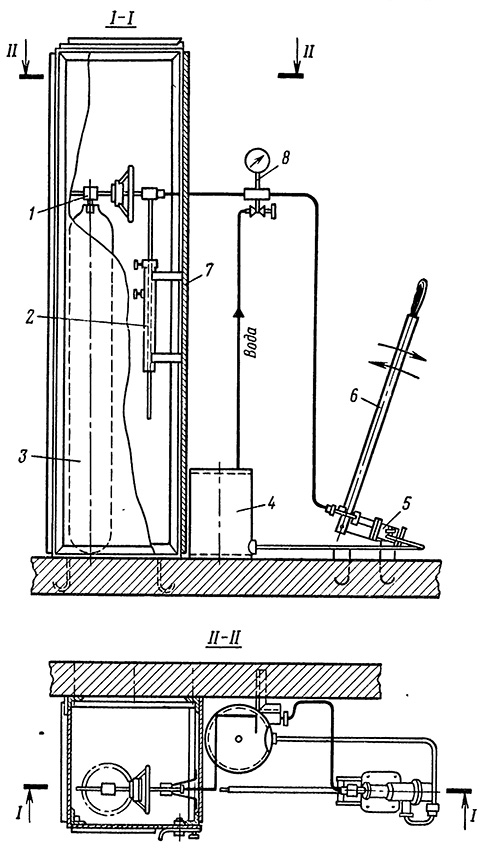
Рис. 84. Стенд для гидравлического испытания баллонов: 1 — штуцер; 2 — передвижная рейка для изменения высоты установки штуцера; 3 — баллон; 4 — бак для воды, 5 — гидравлический насос; 6 — рычаг; 7 — стальной шкаф; 8 — манометр
На рис. 84 показан стенд для гидравлического испытания баллонов. Баллон 3 наполняют водой, ввертывают в него штуцер 1 и присоединяют к гидравлическому насосу 5. Насос приводится в движение рычагом 6 от руки или электродвигателем. Если в стенке баллона имеется дефект (трещина, глубокая коррозия и т. п.), то при испытании баллон может разорваться. Поэтому он устанавливается в стальном шкафу 7 высотой не менее 2 м. Гидравлические испытания баллонов проводят при давлении 1,5 Рр. Продолжительность испытания не менее 1 мин.
Испытуемый объект выдерживает гидравлическое испытание, если сохраняет герметичность (отсутствуют течи и потения в соединениях и на стенках) и не получает видимых остаточных деформаций и признаков разрыва.
В случаях, когда проведение гидравлического испытания сосудов невозможно (большие напряжения от массы воды, трудность ее удаления и т. д.), его разрешается заменить пневматическим испытанием (воздухом или инертным газом) на такое же пробное давление. При пневматическом испытании вентиль на наполнительном трубопроводе от источника давления и манометры выносятся за пределы помещения, в котором находится испытываемый сосуд, а люди удаляются в безопасные места на время испытания сосуда пробным давлением. Под пробным давлением сосуд находится в течение 5 мин, после чего давление постепенно снижают до рабочего и производят осмотр сосуда с проверкой плотности его швов и разъемных соединений мыльным раствором или другим способом.
Пневматические испытания баллонов малой и средней емкости проводят путем их погружения в ванну с водой, при этом давление воздуха в баллоне должно быть равно рабочему. Время испытаний не менее минуты.



Полезная информация: