Методы контроля при герметизации
Безопасность эксплуатации герметичных систем, находящихся под давлением
Безопасность эксплуатации герметичных систем, находящихся под давлением
Осмотру подлежат как наружные поверхности устройств и установок, так и их внутренние (например, внутренние поверхности цистерн). Осмотр сопровождается необходимыми обмерами и измерениями. На основании осмотра делают выводы. Например, в стыковочных сварных соединениях труб смещение кромок не должно превышать следующих максимально допустимых величин:
Толщина стенки трубы, S, мм | Максимально допустимое смещение кромок, мм |
До 3
3-6 6-10 10-20 Свыше 20 | 0,25
0,1S + 0,3 0.15S 0,5S + 1 0,1S, но не более 3 |
Овальность а (%) в любом сечении цидиндрического сосуда определяется формулой
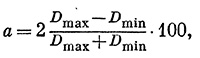
где Dmax и Dmin — соответственно наибольший и наименьший диаметры в одном сечении. В большинстве случаев для цилиндрических элементов, изготовленных из листов и цоковок, а< ±1%.
Овальность (%) трубопроводов сосуда на прямых и гнутых участках определяется соотношением
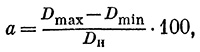
где DH — номинальный наружный диаметр труб, который должен определяться для каждого гиба по результатам измерений или контролироваться при помощи шаблонов (гибы труб подлежат выборочному контролю в количестве не менее 10% от числа гибов одного размера).
Утонение стенки в гнутых участках труб В (%) вычисляется по формуле
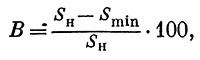
где SH — номинальная толщина стенки прямой трубы, мм; Smin — минимальная толщина стенки в гнутом участке трубы, мм.
Утонение стенки не должно превышать значений, предусмотренных ГОСТ 9842—61. Величина утонения может быть определена, например, измерением толщины стенки после разрезки гибов, производимой в выборочном порядке.
Осмотр сварных швов также сопровождается соответствующими измерениями.
Люминесцентный метод контроля применяется для выявления поверхностных дефектов, главным образом трещин. Он основан на свойстве ряда веществ (люминофоров) издавать собственное свечение (флуоресцировать) под действием ультрафиолетовых лучей. Свойством люминесценции обладают многие минеральные масла. Для увеличения степени их проникновения в различные мелкие трещины к ним обычно добавляют жидкости с малыми коэффициентами вязкости (керосин, бензин, лигроин и др.). Люминофор наносится на поверхность контролируемого изделия. Затем поверхность просушивают теплым воздухом и посыпают порошком (окиси магния, углекислого магния или силикагеля), который извлекает люминофор на поверхность из трещин и частично сам проникает внутрь. Избыточный порошок удаляют с поверхности. После этого контролируемое изделие подвергают облучению в затемненном помещении. Под действием ультрафиолетовых лучей порошок, пропитанный люминофором, флуоресцирует. Трещины выявляются в виде ярко светящихся зигзагообразных линий.
В ультразвуковой дефектоскопии используются ультразвуковые колебания, для возбуждения и регистрации которых при дефектоскопии металлов используют электроакустические преобразователи из пьезоэлектрических материалов (кварца, титаната бария и др.).
Упругие колебания, возбужденные в жидких, газообразных и твердых средах, вызывают распространение упругой волны. При падении ультразвуковой волны на поверхность раздела двух сред в общем случае часть энергии проходит во вторую среду, а часть отражается в первую.
Таким образом, прозвучивая элементы конструкций и исследуя процесс распространения ультразвуковых волн, можно обнаружить внутренние дефекты.
На рис. 81 показана принципиальная Схема электромагнитного метода контроля. Дефектоскоп работает следующим образом. На пьезоэлектрическую пластинку подается кратковременный импульс (1—5 мкс), после чего следует пауза (несколько десятков микросекунд), затем снова импульс и пауза и т. д.
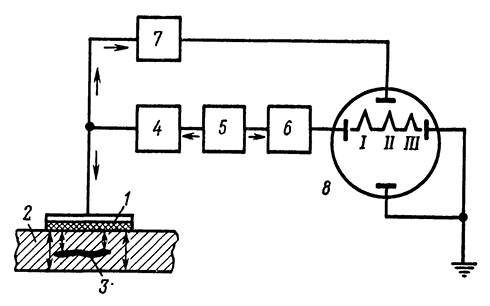
Рис. 81. Схема электромагнитного метода контроля: 1 — пьезоэлектрическая пластина; 2 — исследуемый элемент; 2 — внутренний дефект (трещина); 4 — импульсный генератор; 5 — задающий генератор, 6 — генератор развертки, 7 — приемник-усилитель; 8 — экран электроннолучевой трубки; I — начальный импульс; II — импульс от дефекта; III — данный импульс
В период подачи электрического импульса пьезоэлектрическая пластинка генерирует ультразвуковые волны, в период паузы она преобразует энергию отраженных волн в электрическую, которая после усиления родается в электронно-лучевую трубку и фиксируется на экране последней в виде импульсов:
начального I и донного III (отраженного через всю толщину — до дна исследуемого элемента). При наличии дефекта на экране появляется импульс ТУ от дефекта.
Объем контроля ультразвуковой дефектоскопией устанавливается нормами.
Основные достоинства ультразвукового метода: широкий диапазон контролируемых толщин (от 5 до 500 мм и более), возможность контроля любых металлов и сплавов; высокая производительность (10 см/мин), позволяющая обеспечить 100%-ный контроль. Основные недостатки: невозможность установить характер порока; необходимость иметь гладкую поверхность контролируемого изделия (отсутствие брызг, ржавчин, вмятин); возможность появления ложных импульсов, вызванных неоднородностью контролируемого металла.
Сущность магнитной дефектоскопии (магнитных методов контроля сплошности ферромагнитных металлов) заключается в обнаружении полей рассеяния, образующихся при намагничивании в местах дефектов.

Рис. 82. Схема электромагнитного метода контроля: 1 — контролируемый элемент; 2 — сердечник электромагнита; 3 — обмотка; 4 — усилитель; 5 — сигнализирующее устройство (лампочка)
Методы магнитной дефектоскопии различаются в зависимости от способа обнаружения полей рассеяния: магнитнопорошковый, индукционный и электромагнитный, магнитно-графический методы и др.
Электромагнитный метод" схематично представлен на рис. 82. П-образный электромагнит переменного тока при наличии катушки 3 создает магнитный поток Ф0, который разветвляется на Ф19 идущий через металл сварного соединения, и Ф2, составляющий незначительную часть от Ф0 в том случае, если сварное соединение не имеет пороков:
Если между полюсами электромагнита расположить индукционные катушки 6, то изменение магнитного потока Ф2 вызовет в катушках э. д. с, величину которой можно замерить. Когда пороки недопустимы, срабатывает сигнализирующее устройство.
Магнитные методы контроля пригодны только для контроля ферромагнитных материалов. Метод магнитного порошка применяют при толщине контролируемого изделия 6—7 мм, магнитографический — при толщине менее 12 мм, индукционный и электромагнитный — при толщине менее 18—20 мм. Этими методами контроля практически невозможно установить характер порока и выявить мелкие внутренние трещины.
Контроль (просвечивание) рентгеновскими и гамма-лучами основан на способности рентгеновских и гамма-лучей проникать через непрозрачные тела. Методы контроля различаются в зависимости от способа фиксации дефектов, выявленных лучами. Например, флюороскопический метод заключается в рассмотрении дефектов на экране, фотографический — в фиксации дефектов на фотопленке и т. д.

Рис. 83. Схема контроля рентгеновскими и гамма-лучами: 1 — источник рентгеновских или гамма-лучей; 2 — контролируемый элемент; 3 — кассета; 4 — экран; 5 — пленка; 6 — дефект (трещина)



Полезная информация: