Защита от производственных вибраций. Меры снижения вибраций машин и оборудования. Отстройка от режима резонанса
Для ослабления вибраций существенное значение имеет исключение резонансных режимов, т. е. отстройки собственных частот агрегата и его отдельных узлов и деталей от частоты вынуждающей силы. Определение собственных частот отдельных конструктивных элементов производится либо расчетным путем, либо экспериментально. В первом случае расчет производится по известному значению массы т и упругости q системы.
При экспериментальном определении собственных частот отдельных конструктивных элементов используют специальные стенды, на которых указанные элементы подвергаются внешним знакопеременным силовым воздействиям различных частот. В случае, когда частота динамического воздействия близка к собственной частоте исследуемой колебательной системы, наблюдаются так называемые биения, при которых результирующая амплитуда колебаний (собственных плюс вынужденных) периодически увеличивается или уменьшается. Используя запись колебаний (осциллограмму процесса), можно определять собственные частоты практически любых элементов конструкции.
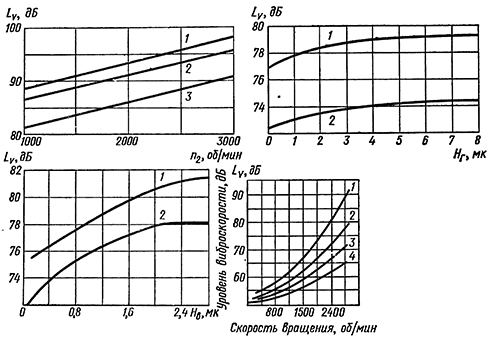
а — скорости вращения n: 1 — № 312; 2 — № 308; 3 — № 305; б — от гранности желоба внутреннего кольца Нг (при разной волнистости Нв): I — Яг = 2-9 мк; 2 — Нг = 0; в — от волнистости (при разной гранности); 1 — Нв = 1-З мк; 2 — Нв= 0-0,5 мк; г — от рода насадки: 1 — вала С, корпуса С; 2 — вала Н, корпуса С; 3 — вала Н, корпуса П; 4 — вала T, корпуса Н
Устранение резонансных режимов при работе технологического оборудования осуществляется двумя путями: либо изменением характеристик системы (массы и жесткости), либо установлением нового рабочего режима (отстройка от резонансного значения угловой скорости wр). Второй метод реализуется на стадии проектирования, так как в условиях эксплуатации режимы работы определяются условиями технологического процесса.
Жесткостные характеристики системы изменяются введением в конструкцию ребер жесткости или изменением ее упругих характеристик.
Вибродемпфирование. Вибродемпфирование — это уменьшение уровня вибраций защищаемого объекта путем превращения энергии механических колебаний данной колеблющейся системы в другие виды энергии.
Анализ выражения (7) показывает, что эффект вибродемпфирования определяется коэффициентом потерь μ, системы, с изменением которого изменяется импеданс системы z.
Увеличение потерь энергии в системе может производиться:
а) использованием в качестве конструктивных материалов с большим внутренним трением;
б) нанесением слоя упруго-вязких материалов, обладающих большими потерями на внутреннее трение;
в) использованием поверхностного трения (например, при колебаниях изгиба двух скрепленных и плотно прилегающих друг к другу пластин);
г) переводом механической колебательной энергии в энергию токов Фуко или электромагнитного поля.
Во всех случаях энергия вибраций непосредственно или после дополнительного превращения переходит в тепловую. Наиболее часто используются первые два способа:
Значения параметра η = wμ/q для основных конструкционных материалов в машиностроении (чугунов и сталей) составляют 0,001—0,01. Как следствие этого, уровни вибрации большинства конструкций в машиностроении достаточно велики. Велика и их вибропроводность.
Значительно большее внутреннее трение имеют так называемые «хайдаметы» — сплавы на основе систем Сu—Ni; Ni—Ti; Ni—Co. В зависимости от амплитуды напряжения в этих сплавах η составляет от 0,02 до 0,1. Большим затуханием обладают (после закалки) сплавы марганца с содержанием 15—20% меди и магниевые сплавы. Детали из этих сплавов имеют меньшую, чем чугуны и стали, вибропроводность. Затухание в металлах сильно увеличивается при повышении температуры.
С точки зрения снижения вибраций наиболее предпочтительным является использование в качестве конструктивных материалов типа пластмасс, дерева, резины. Так, в редукторах используют шестерни из капрона, текстолита и дельта-древесины. В некоторых случаях оказывается возможным также использовать шестерни из твердой резины. В результате происходит снижение вибраций оснований и фундаментов машин, а следовательно, снижается вибрация рабочих мест.
Начат выпуск ручного механизированного инструмента в корпусах из полимерных материалов. Это в значительной мере ослабляет воздействия вибраций на руки работающих.
Широкое применение находят пластмассы при изготовлении технологической оснастки металлорежущих станков: кондукторов, кондукторных втулок, подшипников, зажимных устройств и т. п.
На многих видах оборудования внедряется постановка в подшипниковые узлы вибродемпфирующих втулок, что значительно снижает уровень вибраций.
Указанные мероприятия позволяют улучшить условия труда, что особенно важно на станках с ручной подачей.
На рис.31 показан шпиндельный узел станка с вибродемпфирующей втулкой. Срок службы подшипниковых узлов с вибродемпфирующими элементами значительно выше обычных. Имеются данные, что подшипники прокатных станов с текстолитовыми вкладышами в 10 раз долговечнее бронзовых.
Использование пластмасс в качестве конструктивных материалов позволяет снизить уровень вибрации по виброскорости в широкой полосе средних и высоких частот на 8—10 дБ.
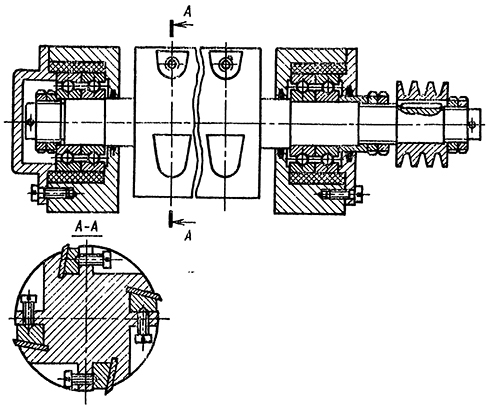
Следует отметить, что при серийном производстве себестоимость пластмассовых деталей оказывается в несколько раз ниже себестоимости металлических деталей.
В том случае, когда применение полимерных материалов в качестве конструктивных не представляется возможным, для снижения вибраций используют вибродемпфирующие покрытия.
Действие покрытий основано на ослаблении вибраций путем перевода колебательной энергии в тепловую при деформациях покрытий. Эффективное действие покрытий наблюдается на резонансных частотах элементов конструкций агрегатов и машин.
В зависимости от значения динамического модуля упругости покрытия подразделяются на жесткие (Е = 108 — 109 Н/м2) и мягкие (Е ≤ 107 Н/м2).
Действие покрытий первой группы проявляется главным образом на низких и средних частотах, второй — на высоких.
На демпфирование жестких покрытий в большей мере оказывает влияние жесткость материала. Чем она выше, тем больше активные потери в системе. Покрытия этого типа рекомендуется выполнять в виде многослойной конструкции. Последние в сравнении с однослойными более эффективны. Особый интерес представляют покрытия из слоя вязкоупругого материала (твердой пластмассы, рубероида, изола, битумизированного войлока, полимерной смеси КЛ-25) и слоя фольги, увеличивающего жесткость покрытия. Коэффициент потерь таких слоистых вибродемпфирующих покрытий составляет 0,15—0,40. Наибольшее распространение из покрытий такого рода получили материалы на основе изола (фольгоизол, стеклоизол, гидроизол). Их отличает дешевизна и достаточно высокая эффективность.
В качестве мягких вибродемпфирующих покрытий используют мягкие пластмассы, материалы типа резины (например, покрытие «Агат»), пластические материалы типа поливинилхлоридного пластика, пенопласт ПХ13-Э и др. Коэффициент потерь этих покрытий лежит в диапазоне 0,05—0,5.
Листовые мягкие вибродемпфирующие покрытия широко применяются в машиностроении, в частности, для снижения уровня вибраций и шума при ручной правке, обработке тонкостенных конструкций малой жесткости на некоторых типах станков.
Однако эксплуатационные качества этих покрытий не всегда удовлетворительны. Так, не представляется возможным обеспечить качественное соединение покрытий с обрабатываемой поверхностью, если последняя имеет сложную конфигурацию. В этом случае используют мастичные покрытия.
Наибольшее распространение получили мастики ВД17-58 и ВД17-59, представляющие собой смесь синтетических смол и наполнителей, а также мастики типа «Антивибрит» на основе эпоксидных смол и др. Коэффициент потерь мастик составляет в большинстве случаев 0,3—0,45. Температурный диапазон при эксплуатации — 20—120° С. Мастики наносятся непосредственно на элементы машин и агрегатов и имеют хорошую адгезию с основным конструктивным материалом. Вибродемпфирующие мастики находят широкое применение в машиностроении для снижения вибраций и шума вентиляционных систем, центробежных компрессоров, насосов, трубопроводов и т. п.
Наибольший эффект вибродемпфирующие покрытия дают при условии, что протяженность вибродемпфирующего слоя соизмерима с длиной волны изгиба в материале конструкции. Это особенно важно при демпфировании низкочастотных колебаний, имеющих большую длину волны. Нанесение покрытий следует производить в местах, где генерируется вибрация максимального уровня. Толщина вибродемпфирующих покрытий практически берется равной 2—3 толщинам демпфируемого элемента конструкции.
Хорошо демпфируют колебания смазочные вещества. Например, масляная ванна значительно снижает уровень вибраций зубчатых зацеплений редукторов, корпусов голтовочных барабанов. Слой смазочного вещества между двумя сочлененными элементами устраняет возможность непосредственного их контакта и, следовательно, появление сил поверхностного трения, которое, как известно, может быть причиной возбуждения вибраций.



Полезная информация: