Техника безопасности при отделке проката.
Безопасность труда при отделке и термической обработке металла
Безопасность труда при отделке и термической обработке металла
Одним из мероприятий, повышающих
качество металла, является
проведение его термической обработки. На всех современных
рельсо-балочных
станах рельсы подвергают замедленному охлаждению или изотермической
выдержке.
Замедленное охлаждение рельсов осуществляется в колодцах, выполненных
огнеупорным кирпичом и имеющих съемные крышки. В этом случае рельсы
охлаждают
на холодильнике до появления магнитных свойств стали, но не ниже
450—500°С, и
затем магнитными кранами загружают в колодцы [1, 29]. Нижний ряд
рельсов
укладывают на подину, а все последующие — на подкладки из
немагнитной стали,
которые позволяют после охлаждения снимать отдельно каждый ряд рельсон
магнитными кранами.
Недостатком замедленного охлаждения рельсов в колодцах является
неравномерность
охлаждения их по высоте и длине колодца, сложность и опасность операций
по
загрузке и выгрузке. Эффективным способом предотвращения образования
флокенов
является изотермическая выдержка при температурах максимальной
подвижности
водорода.
Наиболее
простым методом улучшения свойств рельсовой стали служит повторный
нагрев холодного рельса с последующим охлаждением на воздухе
(нормализация).
Печь для
нормализации рельсов имеет роликовый под с гладкими роликами. Рельсы
движутся в положении «на боку» партиями по
8—10 штук. На участке выдачи,
осуществляемой с помощью шлепперного устройства, свод печи подвесной.
Печь
отапливается доменным газом с индивидуальным подводом газа в каждую из
8 зон. В
последнее время применяется закалка рельсов с прокатного нагрева.
Конструкция
закалочной машины состоит из трех кольцевых коллекторов (по концам и по
середине машины), соединенных с водопроводной сетью. Между коллекторами
укреплено девять труб, в которых через 60—80 мм расположены
специальные
форсунки для распыления воды.
На рис. 9
показана схема поточной линии термической обработки рельсов,
имеющейся на одном из заводов. Готовые «сырые»
рельсы длиной до 25 м со склада
при помощи магнитного крана / подают на стеллаж 2. На рольганге рельсы
комплектуют в пачки по 8—10 шт. (в положение «лежа
на боку») и задают в
закалочную роликовую печь 3. Нагретые рельсы по одному выдают из печи,
кантуют
в положение «стоя на подошве», правят на роликовой
машине 4 и роликами 5 задают
в закалочную машину 6 для объемной закалки в масле. Машина представляет
собой
барабан с горизонтальной осью вращения. По окружности барабана
расположены 12 линий
с каретками для рельсов. При повороте барабана на 30 град, рельс,
нагретый до 850°С, погружают в масло, имеющее
температуру 50—80°С, а с диаметрально противоположной
стороны выдается
закаленный рельс. Па стеллаже 7 закаленные рельсы собирают в пачки (но
12—-18
штук) и направляют в печь 8 для отпуска при температуре примерно
450°С в
течение 2 ч. Далее рельсы охлаждают на холодильнике 13 и правят в
горизонтальной и вертикальной плоскостях на комбинированной
роликоправильной
машине 12. Предусмотрена дополнительная правка рельсов на вертикальных
прессах
11. Выправленные рельсы подвергают инспекторскому осмотру на стеллажах
10,
пакетируют в печи по 25 штук на специальном механизированном устройстве
9 и
затем магнитным 'краном загружают в железнодорожные вагоны или
отправляют на
склад [1, 21, 24].
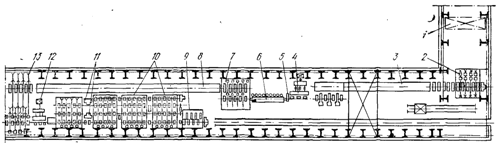
На рис.
10 представлена поточная линия отделки рельсов, предназначенная для
фрезерования торцов, рельсов, сверления отверстий в шейках концов
рельсов,
закалки током высокой частоты поверхностей головок рельсов и выдачи
готовых
рельсов на инспекторский стеллаж. Поточная линия состоит из следующего
оборудования: контактного шлеппера—для передачи рельсов с
рольганга на цепной
транспортер (шлеппер имеет шлепперные тележки специальной конструкции,
автоматически устанавливающие/рельсы на расстоянии 500 мм друг от
друга)
центрователя — для автоматического деления пополам припуска
на обработку торцов
рельсов между правым и левым фрезерными станками; кантователя
— для кантовки
рельсов на 90 град, в начале и в конце поточной линии.
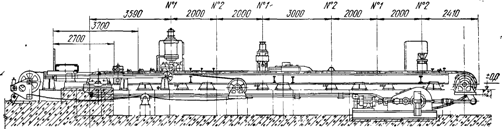
Выправленные рельсы по рольгангу подают к поточным линиям отделки и
канатными
шлепперами укладывают на стеллажи перед фрезерными станками. Со
стеллажей
рельсы подают к фрезерным станкам, а затем к сверлильным станкам и
установкам
для высокочастотной закалки. На фрезерных станках рельсы автоматически
зажимаются гидравлическими зажимами и фрезеруются одновременно с обоих
концов.
Затем рельсы автоматически подаются гидравлическими вталкивателями к
сверлильным станкам, где их зажимают и сверлят отверстия. После этого
рельсы
подают к установкам последней отделочной операции —
высокочастотной закалки
концов рельсов.
Для
проведения закалки концов рельсов имеются специальные кабины, каждая из
которых предназначена для закалки одного конца рельса. В этих кабинах
на конец
рельса надевают индуктор, подключенный к высокочастотному генератору.
После
нагрева конца рельса индуктор выключается и включается охлаждающая
жидкость —
вода или эмульсия. Отдельные рельсы поступают на рольганг, по которому
их
передают на инспекторские стеллажи, где производят окончательную
приемку
рельсов. После инспекторской приемки рельсы поступают на склад готовой
продукции для отгрузки. Балки, швеллеры и другие профили сортовой
стали,
прокатываемой на рельсо-балочных станах, после резки на мерные длины на
салазковых пилах и охлаждения на холодильнике поступают в специальное
отделение, где подвергаются различным отделочным операциям [1].
Для
правки балок, швеллеров и других профилей в этом отделении
устанавливают
такие же роликовые правильные машины, как и для правки рельсов. Для
правки
сортовой стали в плоскости большей жесткости и для доправки концов
полос, не
выправленных на роликовой сортоправильной машине, устанавливают
горизонтальные
правильные прессы.
Для резки
проката на мерные длины и вырезки брака после осмотра профилей на
инспекторских стеллажах устанавливают ножницы холодной резки. Укладка в
штабеля
сортового проката производится штабелирующей машиной, состоящей из
сварной
рамы, перемещающейся по рельсам на четырех колесах с установленным на
ней
подъемным столом [29]. Для кантовки сортового проката на инспекторских
стеллажах применяют кантователь.
К
отдельным операциям при горячей прокатке листовой стали относят правку,
охлаждение, резку, термическую обработку, удаление поверхностных
дефектов и др.
В зависимости от типа стана и программы прокатки отделочные операции
выполняют
на оборудовании, установленном в потоке технологического процесса [31].
Правку
толстолистовой стали производят в горячем состоянии. Холодную правку
листов применяют только для листов, не выправленных при горячей правке.
Для
правки листовой стали применяют многороликовые правильные машины.
Охлаждение толстолистовой стали на современных листовых станах
происходит при
транспортировке по рольгангам, роликовым цепным транспортером и
стеллажам-холодильникам. Стеллаж-холодильник для охлаждения листов
состоит из
настила плит цепного шлеппера с приводом, подводящего и отводящего
рольгангов.
После охлаждения листы осматривают с обеих сторон на инспекторском
столе,
оборудованном кантователем для кантовки листов на 180 град. После
охлаждения и
осмотра производят резку листов на дисковых ножницах двухпарных или
многопарных.
В
современных листопрокатных цехах, выпускающих качественную углеродистую
и
легированную листовую сталь, широко применяют термическую обработку
—
нормализацию, которая производится для снятия наклепа, получающегося
при низкой
температуре листа в конце прокатки. На некоторых листовых станах
линейного типа
печи для нормализации горячекатаной толстолистовой стали устанавливают
за
станом в основном потоке технологического процесса. Печь для
нормализации
располагается в этом случае параллельно с рольгангом зароликовой
правильной
машиной.
Листы подаются к печи с помощью
шлепперов [31, 221 -На большинстве
станов печи для нормализации устанавливают /вне основного
технологического
потока. В этих случаях эти печи применяют также и для закалки с
отпуском.
Наибольшее распространение получили проходные печи с роликовым подом.
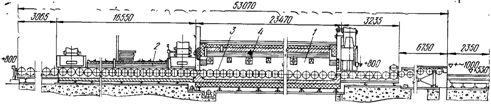
1 - зона нагрева; 2 - зона охлаждения; 3 - роликовый под; 4 - горелка.
На рис.
11 показана печь с роликовым подом, предназначенная для нормализации
листов толщиной 6—25 мм и нагрева под закалку листов толщиной
12—25 мм. Для
нормализации листы из печи выдаются на рольганг, по которому они
поступают к
правильной машине. После правки листы передают на стеллажи для
охлаждения; затем
их укладывают в стопы и передают мостовым краном на склад. Если же в
этой печи
производят нагрев листов под закалку, то из печи лист быстро подают в
закалочный пресс. После закалки листы проходят отпуск, который
может
проводиться в такой же печи, но имеющей две системы отопления: одну
— для
нагрева листов под нормализацию или закалку, вторую— для
нагрева до температуры
отпуска.
Часто отпуск производят в отдельной
печи, установленной за печью для
нормализации и закалки. В печах такого же типа производят нагрев под
закалку
листов из нержавеющей стали. Отжиг листовой стали в современных
листопрокатных
цехах горячей прокатки производят обычно в колпаковых печах. В
последнее время
в цехах холодной прокатки листовой стали устанавливают также для отжига
колпаковые
печи.
При
отжиге металла может произойти травмирование рабочих при
транспортировке
металла, коробов с листами, а также колпаков и муфелей колпаковых
отжигательных
печей и ожоги нагретым металлом [31].
Для
предотвращения травм при отжиге металла все операции по подаче, выдаче
и
транспортировке термически обрабатываемого металла выполняют при помощи
кранов,
толкателей, лебедок или других соответствующих механизмов.
Помещения, где производится термическая обработка металла, оборудуют
эффективной системой аэрации, исключающей повышение температуры в цехе.
Отжигательные печи с газовым отоплением должны соответствовать
требованиям
правил безопасности в газовом хозяйстве металлургических заводов. Новые
и
реконструируемые отжигательные печи желательно выполнять в виде
конвейерных
печей с шагающим подом и в отдельных помещениях или в помещениях
(пролетах,
участках), изолированных от других участков цеха, так как выделяемое
тепло при
остывании рулонов или коробов с листовым металлом выделяет избыточное
тепло,
отрицательно влияющее на организм работающего. Остывающие короба должны
устанавливаться в один ряд. Установка коробов в два ряда может быть
допущена
только в старых цехах из-за недостатка свободных площадей. При этом
необходимо
следить, чтобы верхние короба устойчиво лежали на двух нижних. Короба,
поддоны
и муфели с обгоревшими проушинами или приливами для захвата их краном
заменяют
новыми.
Колпаковые печи для удаления продуктов сгорания имеют вытяжную систему
и свечи,
выведенные из помещения. Вывод нейтрального газа из-под муфеля в
помещение цеха
запрещается. Подвалы, расположенные под колпаковыми печами, оборудуют
надежно
действующей приточно-вытяжной вентиляцией. Поддоны печей располагают на
расстоянии не менее 2 м друг от друга, при этом проходы не должны
загромождаться
Колпаками, муфелями, коробками, пачками металла и др. Колпаки и муфели
оборудуют надежными /Приспособлениями при их перемещении кранами без
применения
ручной прицепки и отцепки.
Подключение газа к отдельным колпакам, зажигание газа, отключение и
ремонт
газопроводов производят по специально составленной инструкции с учетом
мер
предосторожности, предусмотренных Правилами безопасности в газовом
хозяйстве.
При этом должны быть отражены следующие моменты:
- плотность прилегания муфелей, обеспечивающаяся устройством песочных затворов;
- давление газа в подвалах перед горелками должно быть не менее 50 мм вод. ст. При падении давления отопление печей прекращается;
- при всяких остановках одной печи или кратковременных остановках группы печей их следует отключить, а затворы залить водой. В случае остановки группы печей на длительный период следует после отключения и наполнения водой затворов перед каждой печью наполнить водой общий затвор, установленный перед всей группой печей;
- перед пуском газа после остановок, связанных с отключением подводов газа к печи, эти подводы предварительно тщательно продувают паром или газом через свечи при плотно закрытых затворах. Все подводы газа к печам должны быть герметичными, исключающими просачивание газа в помещение, где находятся печи.
Первоначальный пуск газа при разогреве
печи производят под руководством и
надзором ответственного лица. Во избежание образования гремучей смеси
муфельную
печь перед разжиганием продувают нейтральным газом [5, 28].
Устройство электрических отжигательных печей предусматривает соблюдение
всех
правил электробезопасности. Все электровводы и выводы имеют жаростойкую
изоляцию. Стенды, на которые устанавливают колпаки, надежно заземляют.
Отжигательные и нормализационные электропечи обеспечивают специальными
электроизоляционными прокладками, исключающими контакт металла с
нагревательными элементами.
Конвейерные или с шагающим подом нормализационные печи имеют устройства
(роликовые затворы, паровые завесы, вытяжные зонты и др.), которые
исключают
возможность просачивания продуктов сгорания и нейтрального газа в
помещение,
где расположены печи.
Установки
для непрерывного отжига полосы обеспечивают устройствами,
предотвращающими обрыв полосы, и приспособлениями для ее проводки на
случай
обрыва; светозвуковой сигнализацией, оповещающей о пуске механизмов
печи;
аварийными выключателями около основных агрегатов установки. Все
опасные части
приводов непрерывной установки закрывают оградительными устройствами.
Переходные площадки через линию непрерывной установки делают с перилами
высотой
не менее 1,1 м и бортами снизу высотой не менее 180 мм.
Контроль
за состоянием полосы в печи непрерывного действия должен
обеспечиваться автоматически.
Для
безопасной эксплуатации установки приготовления нейтрального газа,
применяемого для зеркального отжига листов, руководствуются правилами
безопасности в газовом хозяйстве металлургических заводов и местными
инструкциями по безопасному обслуживанию этих устройств.
При
охлаждении водой полов или листов после отжига применяют устройства,
исключающие попадание пара и брызг воды в помещение. Кабины машинистов
кранов
термического отделения оборудуют приточной вентиляцией с подачей
охлажденного
воздуха или применяют дистанционное управление [5].



Полезная информация: